2. Assessment of the supply chain
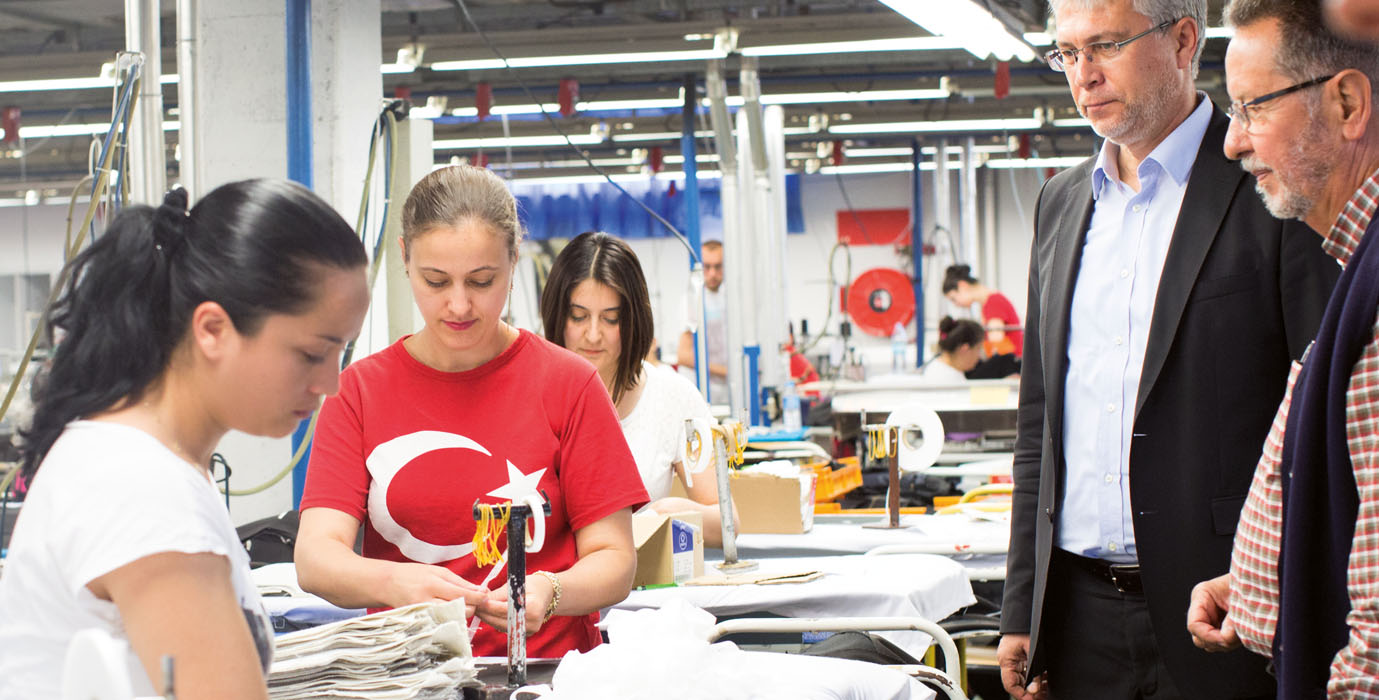
The assessment and analysis of the supply chain provides knowledge on the type of supply chain Inditex employs, its strengths, and the areas where it can be improved. To this end, the compliance programme ensures that all of Inditex’s suppliers observe the Code of Conduct for Manufacturers and Suppliers, and that they implement Corrective Action Plans where improvements are needed in their production chain if they are to continue to as part of Inditex’s supply chain. Moreover, we consider that the participation of the supply chain workers is fundamental, and actively advocate such involvement through the implementation of several programmes.
Audit types
In 2015, Inditex carried out 10,977 audits with the aim of getting to know, assess and improve its supply chain. All suppliers and manufacturers in our supply chain are subject to regular audit processes, which commence as soon as trade relations with Inditex through an initial pre-assessment audit. Once suppliers have started working with Inditex, they must undergo social audits, special audits and traceability audits periodically.
Evolution of audits carried out over the last five years
- Pre-assessment consists of a preliminary evaluation of potential suppliers and factories performed by internal or external auditors without prior notice. Only those meeting the requirements established by Inditex in its Code of Conduct can enter the supply chain. From that moment on, they are subject to the Code of Conduct and to the standards set out in the Inditex Minimum Requirements document.
- Social audits to verify the degree of compliance with the Code of Conduct and to establish Corrective Action Plans (CAPs) intended to ensure respect for fundamental labour rights. Social audits can take the form of initial or follow-up audits.
- Special audits consist of visits and inspections related to specific issues such as the health and safety of workers, and competence visits to ensure compliance with the Corrective Action Plans. These audits also include inspections of washing processes to ensure that practices banned by Inditex, such as sandblasting, are not in use.
- Traceability audits are used to verify the traceability of the supply chain based on the analysis of information gathered via the Manufacturer Management System.
Audits performed on manufacturers in 2015 by geographic area and audit type
Social | ||||||
---|---|---|---|---|---|---|
Geographic area | Pre-Assessment | Initial | Follow-up | Special (*) | Traceability | Total |
Africa | 79 | 105 | 73 | 375 | 542 | 1,174 |
America | 113 | 64 | 396 | 57 | 1,642 | 2,272 |
Asia | 1,420 | 918 | 958 | 1,069 | 609 | 4,974 |
Europe (non-EU) | 497 | 237 | 271 | 20 | 40 | 1,065 |
European Union | 594 | 471 | 331 | 63 | 33 | 1,492 |
Total | 2,703 | 1,795 | 2,029 | 1,584 | 2,866 | 10,977 |
(*) Special audits include, among other aspects: health and safety verification and competence visits to evaluate the degree of compliance with the Corrective Action Plans.
Compliance Programme
The aim of the Compliance Programme is to ensure that labour conditions comply with international standards and Inditex’s Code of Conduct for Manufacturers and Suppliers.
A first assessment takes place before the supplier has entered the supply chain with a pre-assessment audit. In 2015, some 2,703 pre-assessment audits were performed on potential suppliers and factories, of which 88% had a positive outcome. This first filter allows only manufacturers that comply with the standards established in the Code of Conduct to enter the supply chain. From the moment they enter Inditex’s supply chain, they assume responsibility for complying with the Code of Conduct.
Pre-assessment audits 2015
Geographic area | Pre-assessment audits | % deemed Approved |
---|---|---|
Africa | 79 | 78% |
America | 113 | 79% |
Asia | 1,420 | 84% |
Europe (non-EU) | 594 | 95% |
European Union | 497 | 95% |
Overall total | 2,703 | 88% |
The percentage of positive outcomes from pre-assessment audits increased in 2015 over the previous year, and this highlights that supplier premises are demonstrating ever-increasing levels of commitment and responsibility when it comes to labour standards.
Once suppliers have been admitted into the supply chain, social audits allow them to be classified according to degree of compliance, identifying any corrective actions that must be implemented. Regardless of any other visits and programmes undergone, each factory is audited periodically. Visit frequency varies according to compliance level and a case-by-case analysis.
Social audits by geographic area in 2015
Geographic area | Initial | Follow-up |
---|---|---|
Africa | 105 | 73 |
America | 64 | 396 |
Asia | 918 | 958 |
Europe (non-EU) | 237 | 271 |
European Union | 471 | 331 |
Total | 1,795 | 2,029 |
In 2015, Inditex auditors performed 3,824 social audits that made it possible to assess the degree of compliance with the Code and establish Corrective Action Plans for areas requiring improvement.
Percentage compliance with the Code of Conduct in active factories (*) associated with suppliers with purchase in 2015
(*) Does not include factories rejected in 2015.
(**) Includes the lack of suitable systems for checking the age of workers.
(***) Includes the lack of suitable systems for registering and informing workers.
Following the performance of social audits, factory compliance with each of the various sections of the Code of Conduct is analysed to identify areas for improvement and establish specific programmes to achieve improvements. It is worth highlighting that percentage compliance with wages in Asia and America rose overall in 2015. This increase is the result of the work of the range of sustainability teams and their close collaboration with suppliers to improve the working conditions of workers in the supply chain.
Social audits classify suppliers into four categories depending on their level of compliance with the Code of Conduct. The percentage of A and B rated suppliers rose by 3% over the previous year, evidence of our suppliers’ commitment to improvement and the positive result of the programmes created by Inditex’s teams, confirming the trend for improvement in supplier ratings seen over the last five years. Moreover, suppliers with an A or B classification accounted for some 95% of production.
In 2015 there were also 1,500 special audits that examined specific issues such as the health and safety of workers, or the verification of compliance with the Corrective Action Plans.
Classification of suppliers with purchase in 2015 *
2015 | 2014 | |||
---|---|---|---|---|
Supplier classification* | Suppliers | % Suppliers | Suppliers | % Suppliers |
A | 724 | 42% | 678 | 42% |
B | 794 | 46% | 699 | 43% |
C | 116 | 7% | 133 | 8% |
PAC | 35 | 2% | 54 | 3% |
PR | 56 | 3% | 61 | 4% |
Overall total | 1,725 | 100% | 1,625 | 100% |
*Supplier A: complies with the Code of Conduct
Supplier B: breaches a non-material aspect of the Code of Conduct
Supplier C: breaches a sensitive aspect of the Code of Conduct
Supplier subject to Corrective Action Plan (CAP): supplier that breaches critical aspects of the Code of Conduct, requiring the immediate implementation of a Corrective Action Plan
PR supplier: undergoing an auditing process.
Classification of supplier ratings over the last five years
((*) Supplier A: complies with the Code of Conduct
Supplier B: breaches a non-material aspect of the Code of Conduct
Supplier C: breaches a sensitive aspect of the Code of Conduct
Supplier subject to Corrective Action Plan (CAP): supplier that breaches critical aspects of the Code of Conduct, requiring the immediate implementation of a Corrective Action Plan
PR supplier: undergoing an auditing process.
Commitment to living wages in the supply chain
The Inditex Code of Conduct for Manufacturers and Suppliers establishes that a decent wage “should always be enough to meet at least the basic needs of workers and their families and any other needs which might be considered as reasonable”.
Inditex has worked in conjunction with IndustriALL Global Union, the University of Northumbria and Cambridge University’s Centre for Business and Public Sector Ethics to develop an assessment methodology that brings together precise and innovative evidence and procedures to drive the payment of living wages throughout Inditex’s supply chain. This remains a flagship project in the sector today.
This methodology is subject to an ongoing review process to incorporate the improved practices identified over the years during the implementation of various projects. Thanks to a number of projects, which we detail below, we have seen progress on wages within Inditex’s supply chain, in particular in Asia and America.
Evolution of compliance with the Code of Conduct in active factories on matters of wages
Projects
Promoting collective bargaining
The commitment of manufacturers and suppliers to paying a living wage is firmly enshrined in the Global Framework Agreement signed with IndustriALL, which aims to guarantee respect for human rights in the social and labour spheres through the promotion of decent work in the whole of Inditex’s supply chain.
LCollective bargaining represents a fundamental tool in relations with workers and the promotion of social dialogue within companies supplying Inditex. In order for bargaining processes to be effective in driving the negotiation of fair working conditions (including living wage levels), there must be worker representation as the result of free elections. This is an activity that Inditex has actively promoted. For example, Inditex has worked with IndustriALL in Turkey and Bangladesh clusters to organize elections of worker representatives in 12 factories over the last two years. Moreover, Inditex is involved in the Accord pilot project in Bangladesh to create health and safety committees to represent workers.
Ongoing work with IndustriALL Global Union and its local affiliates seeks to achieve goals such as guaranteeing independent elections of worker representatives. In 2015, this work extended to five factories in Portugal, two in Cambodia, four in India, five in Vietnam, four in Bangladesh and six in Turkey.
Number of factories involved in IndustriALL programmes
2014 | 2015 | |
---|---|---|
Number of factories involved | 5 | 26 |
Number of workers | 3,478 | 32,751 |
Responsible purchasing practices
Purchasing practices have a direct impact on the working conditions of supplier employees, including on their remuneration.
In this sense, identifying and explaining the implications of certain commercial decisions is a way of ensuring that workers receive fair wages for the work they carry out to produce the products subsequently sold in our stores.
To this end, Inditex actively promotes the regular training of purchasing teams in each of its brands by the Group’s sustainability teams.
Evolution of internal training
Improved working methods and systems
One of the ways of achieving wage increases is by improving working methods. Various pilot projects have been implemented such as in China – one in collaboration with the International Labour Organization (ILO), and in Turkey with assistance from IndustriALL. These projects have demonstrated that better work organization leads to increased productivity and efficiency, which in turn bring improved conditions for workers, not only in terms of wages but also in terms of working environment. For example, in one factory in China, such where a training project resulted in improved productivity and the quality of management processes. These, among other improvements, led to an increase in employee wages.
Improved productivity in factories is not an end in itself in the sphere of sustainability; rather, it must be accompanied by the promotion of social dialogue in factories. To this end, workers and their representatives must be actively involved, along with factory management, in deciding on incentive systems and improvements to working conditions.
Collaboration with other stakeholders
Inditex alone has limited capacity to change the working conditions across its entire supply chain. Therefore, the active involvement of local trade unions, suppliers, governments, NGOs and other representatives of civil societies is needed in order to drive a real impact on working conditions among factories producing for Inditex.
In this regard, Inditex continues to work with IndustriALL and other brands in a number of initiatives such as ACT (Action, Collaboration, Transformation) which aims to drive increases in worker wages. As a result, active efforts have been made that have yielded various joint interventions on the ground, including in Cambodia, where it is hoped advances will continue to be made to promote mature industrial relations between worker and employer representatives.
Support campaigns
Inditex has publicly expressed its commitment to improving wages and the respect for laws governing freedom of association and the right to collective bargaining in countries such as Cambodia, where in June 2015, via the ETI, the Group expressed its concern for issues regarding respect for ILO Convention 87 and 98 with the country’s new labour legislation.
Worker participation
Worker participation in the supply chain is considered a core principle at Inditex, and this is reflected in the Framework Agreement signed with IndustriALL Global Union in 2007 and renewed in 2014. Inditex shares all information on its supply chain with IndustriALL. This information is updated on a regular basis. Moreover, Inditex regularly works with IndustriALL representatives, local trade unions and workers with the core objective of establishing and promoting initiatives involving the training and representation of workers in the supply chain. In 2015, the implementation of the Framework Agreement took the form of specific activities mainly in Portugal, Vietnam, Cambodia, India, Turkey and Bangladesh.
Number of factories involved in IndustriALL programmes in 2015
2015 | |
---|---|
Number of factories visited | 26 |
Number of workers | 32,751 |
The establishment of Works Councils within Inditex’s supply chain
In 2015, Inditex and the international trade union federation IndustriALL initiated a pioneering project in Bangladesh that aimed to guarantee the legitimate participation of workers in works councils in factories supplying to Inditex.
Four factories were selected from Inditex’s supply chain in Bangladesh to take part in a pilot project with this objective in mind. During the first phase of the project conducted in collaboration with IndustriALL, the processes used for the constitution of “participation committees”, which are equivalent in Bengali legislation to works councils, was monitored in these factories.
This process covered aspects including the free selection of candidates by workers and democratic elections.
The Bangladesh experience was especially valuable since it guarantees workers free access to participation committees while also offering guarantees for adequate worker representation in the establishment of occupational health and safety committees. As set out in national legislation, members of these committees must come from a prior selection from the company’s participation committee.
This last measure is particularly important given that the Accord, of which Inditex is an original signatory, establishes a pledge for all members of the Accord that establishes democratic occupational health and safety committees in all of the factories that work for them.
Corrective Action Plans
Following a social audit, Inditex establishes Corrective Action Plans for each factory, regardless of the ranking they have obtained. These plans are monitored by local sustainability teams, who provide support and assistance to suppliers and manufacturers so that they can remedy the breaches detected during the audit, implementing the measures detailed in the plan. Other parties such as trade unions and NGOs may support or oversee the improvement measures.
In the case of breaches of sensitive aspects of the Code of Conduct, such plans come under the name Project D, in which a far stricter monitoring process takes place to monitor the corrective measures stipulated for a maximum duration of six months. Once that period has expired, a new social audit is performed to verify compliance. If a supplier or manufacturer does not manage to fulfil their Corrective Action Plan, relations will be severed, and the manufacturer or supplier in question will no longer be able to form part of Inditex’s supply chain.
Inditex considers continual improvement to be a fundamental aspect of achieving a stable and sustainable supply chain; with this in mind, the Corrective Action Plan method is designed to give suppliers and manufacturers the chance to make improvements.
In 2015, a total of 510 Corrective Action Plans were implemented, of which 64% were completed successfully. This percentage represents an increase in the success rates over previous year (59% success rate), an improvement that can be attributed to the efforts of local sustainability teams and suppliers to ensure the implementation of the improvements proposed. With a view to the completion of Corrective Action Plans, Inditex’s internal teams performed 1,124 competence visits to factories to ensure that the improvements were being implemented, as well as to offer guidance. These plans also received assistance from a range of organizations including the Association for the Support of Contemporary Living in Turkey and Pratham in India.
Corrective Action Plans 2015
Geographic area | Factories that initiated an improvement process | Factories that improved their compliance | Factories in the process of improvement | Percentage of CAPs successfully completed |
---|---|---|---|---|
Africa | 10 | 5 | 5 | 100% |
America | 120 | 34 | 71 | 69% |
Asia | 244 | 105 | 83 | 65% |
Europe (non-EU) | 77 | 14 | 49 | 50% |
European Union | 59 | 23 | 20 | 59% |
Total general | 510 | 181 | 228 | 64% |
Development of a Corrective Action Plan
Of the 1,725 suppliers with purchase in 2015, some 65 were rejected and no longer formed part of Inditex’s supply chain by 31 January 2016. Suppliers might be rejected for purely commercial reasons or relations severed due to some kind of breach of the Code of Conduct. These figures demonstrate the adherence in purchasing decisions to sustainability criteria: only those suppliers and manufacturers that comply with Inditex’s social, environmental, and product health and safety policies can continue to form part of the supply chain.
Suppliers rejected in 2015
Geographic area | Suppliers with purchases* | Rejected due to breach of the Code of Conduct | Rejected for commercial reasons | Active suppliers at 31/01/2016 |
---|---|---|---|---|
Africa | 130 | 0 | 0 | 130 |
America | 74 | 7 | 6 | 61 |
Asia | 836 | 12 | 22 | 802 |
Europe (non-EU) | 185 | 13 | 0 | 172 |
European Union | 500 | 3 | 2 | 495 |
Total | 1,725 | 35 | 30 | 1,660 |
(*) Suppliers of fashion items, mainly clothing, footwear and accessories, with a production for Inditex of over 20,000 units/year. Suppliers with smaller production account for 0.37% of the total production.