Advances in the evaluation and control of wet processes
At Inditex, we are working to ensure more sustainable production processes and to achieve zero discharge of hazardous substances by 2020, through continuous improvement of the supply chain. To achieve this, in the area of wet manufacturing processes (dyeing, printing, washing, tanning and finishing) we have designed and implemented our own programmes to regulate the facilities and processes that use these substances, in order to guarantee the health and safety of the products and to ensure that they are produced in a clean manner. Green to Wear is the standard that seeks a cleaner, more environmentally friendly production process with less intensive consumption of natural resources; while Ready to Manufacture is the code of good manufacturing practices that ensures compliance with both the product health standard Clear to Wear and the List of Restricted Manufacturing Substances in wet process facilities.
Green to Wear
At Inditex we believe that achieving a more sustainable supply chain and reduced natural resources consumption demand a commitment to continuous improvement. Since we implemented the Green to Wear internal standard in 2014 with the aim of achieving more sustainable production practices and less intensive resource consumption, we have continued to make progress in identifying the best techniques available in wet processes, in order to incorporate them into our supply chain.
We continue working to ensure that our suppliers follow the Green to Wear standard in their wet processes, by means of specific technical training projects. In 2015, participation in these projects by near to 200 direct suppliers and 404 wet process plants has led to improved traceability and environmental performance in our supply chain. This has been achieved by applying practical measures that enhance the sustainable management and efficiency of wet process plants in the following areas: raw materials, water, technology and processes, chemical products, waste water, waste and energy.
Moreover, through our collaboration agreement with the University of A Coruña, we have developed training materials on the different water purification systems, to help improve the water purification stations used by our suppliers. These support materials, available on the Water Master Plan website in Inditex’s supply chain, enable suppliers to optimize the performance of their waste water purification systems and to improve minimization at source of undesirable substances that may be detected in the discharge. For example, the support guide for the manufacturing of sustainable products has provided wet process facilities with valuable technical and practical information for the correct implementation of the Green to Wear standard.
We also work with the University of A Coruña on analysing the most important chemical substances present in textile wastewater. This task allows us to continuously improve the methodology on which the Green to Wear standard is based, and moves us further towards our target of zero discharge. The findings from this analysis and other collaborations for supply chain technical training are published on the Water Master Plan website: www.wateractionplan.com.
Our teams also check that wet process facilities have correctly sized and installed waste water purification stations, and that they are adequately managed and meet the established discharge parameters. The correct installation and appropriate management of a standard purification station in the textile industry also allows some of the treated water to be reused, mixing it with clean water and then using it again in the wet process. This practice is among those that our suppliers must follow in order to be classified as Right to Wear+ in our environmentally sustainable production standard for Green to Wear products.
The results of our supply chain’s waste water analyses are publicly available, on the website of the Water Master Plan in the Inditex supply chain. We also encourage our suppliers to disclose the results of their waste water analyses, in particular in China on the Institute of Public and Environmental Affairs of China (IPE) website, which includes information on the situation of factories and promotes their improvement. We also work with the IPE to improve the environmental behaviour of wet process facilities in China by promoting the implementation of corrective measures to resolve any environmental breaches.
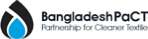
Partnership for Cleaner Textile in Bangladesh – PaCT
Inditex participates actively in the Partnership for Cleaner Textile in Bangladesh (PaCT) programme, which seeks to improve the wet processing sector in Bangladesh, contributing to the wellbeing of its workers and the community, and promoting their long-term competitiveness.
Through this programme, we have not only achieved reduced water-consumption, but have also improved the quality of the discharged water. To this end, we work jointly with the World Bank to disseminate technical knowledge and to provide access to funding for cleaner production processes.
Involvement in this programme by a large part of our supply chain in Bangladesh has enabled 13.4 million cubic metres of water a year to be saved and has avoided the emission of 169,400 tonnes of CO2 and the discharge of 10.6 million cubic metres of waste water.
Ready to Ready to Manufacture: Wet processes for safe products
Inditex has increased its product safety requirements and environmental commitments across its manufacturing processes by developing and implementing its code of good manufacturing practice: Ready to Manufacture.
Where The List, by Inditex is the tool we use for the monitoring, control and classification of chemical substances used in the manufacture of our products, Ready to Manufacture is the programme designed and implemented by Inditex to control the facilities and processes that use restricted substances.
The programme includes a guide to good manufacturing practices, aimed at reducing the risk of non-compliance with the product safety standard and the List of Restricted Manufacturing Substances in facilities using wet processes (dyeing, tanning, printing, finishing and washing). It also includes a training and auditing protocol for the facilities that form part of the value chain, allowing the implementation model to be adapted to the specific conditions at each facility and to the level of experience of its personnel.
Since the programme began in 2013, some 335 direct suppliers have been trained and 1,506 facilities audited.