3. Optimization of the supply chain
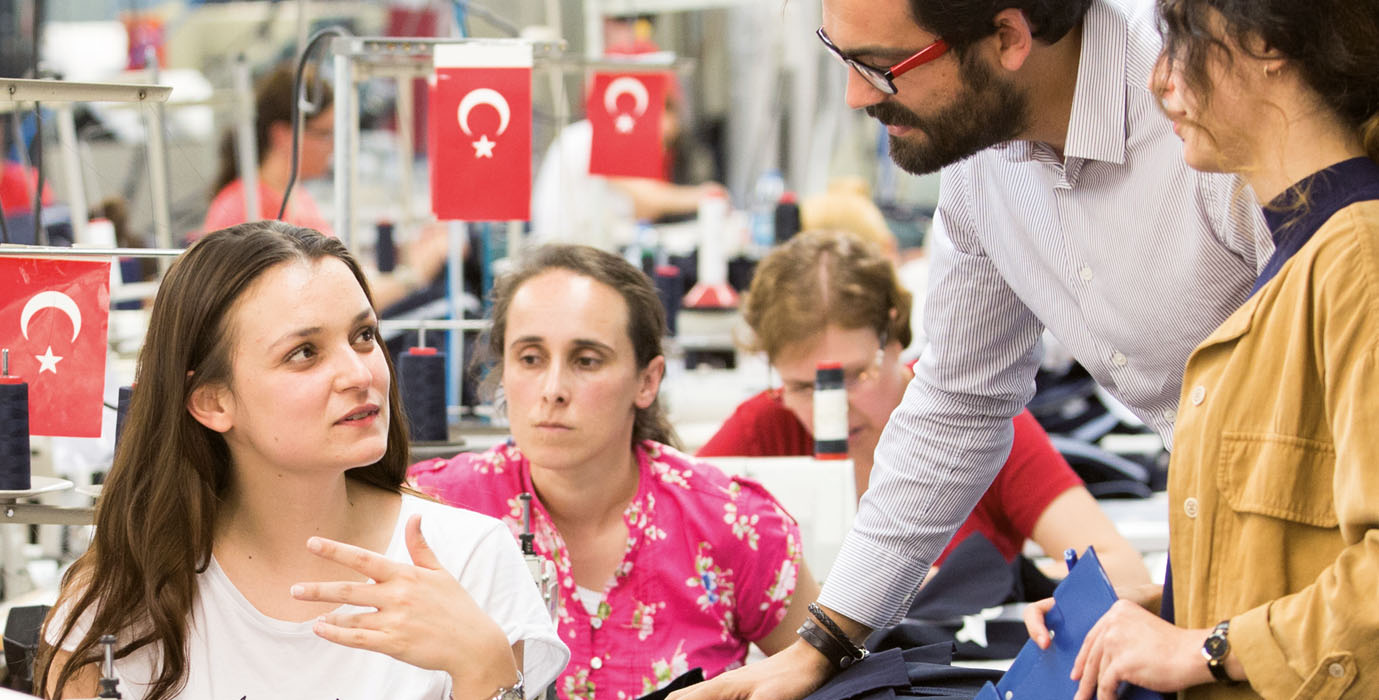
Inditex understands that it must help its suppliers to improve their production conditions and support them in this process throughout their commercial relationship, with the goal of ensuring sustainability in the supply chain. To this end, the Group implements a range of initiatives and projects that aim to improve the effectiveness of audits, train suppliers and consolidate a stable supply chain.
Responsible purchasing practices
Inditex’s commitment to sustainability goes beyond supplier assessment, and in this respect internal awareness-raising among purchasing teams is a priority.
Along with the Compliance Programme and strategic selection of suppliers, a responsible approach to purchasing practices is a vital part of achieving a more sustainable supply chain.
Purchasing practices encompass various aspects of strategic planning within the Purchasing Department that range from logistics and the purchasing process itself to the values and principles underlying the decisions made by purchasing teams.
Throughout 2015, regular specific training activities have taken place involving purchasing teams. These activities aimed to raise awareness as to how purchasing decisions can impact on the factories used for production, thereby advancing towards the introduction of a system of specific training on responsible purchasing practices at the corporate level.
This kind of session seeks to broaden knowledge on sustainability and the Inditex Code of Conduct for Manufacturers and Suppliers and promote the advantages offered by a sustainable purchasing strategy.
Inditex collaborates with other brands, sharing its experience and designing joint actions for the application of responsible purchasing practices.
Effective auditing
The information gathered during audits is crucial to Inditex’s purchasing teams. Therefore, collaboration between the Group’s sustainability teams and all other Inditex departments is essential to ensuring that audits – and, more generally, all of the tools used to ensure the responsible management of the supply chain – are interconnected and effective.
In this sense, it is important that purchasing teams are informed of the results of audits and are involved in supplier improvement processes.
All of Inditex’s departments participate in the sustainability strategy, and so training and capacity building are fundamental, in particular in the case of the Group’s purchasing department.
In June 2015, two training sessions were held at the company’s central offices, attended by 434 Inditex employees. The main objective of these sessions was to disseminate the work of the Group’s sustainability teams in the range of countries where they are based and carry out their activities. Local teams told attendees about the work they carry out with real examples of projects developed in their regions. Their experiences were also reflected in a lengthy article published in the company’s internal magazine distributed throughout the Group’s offices and stores.
Meanwhile, during the course of 2015, a total of 12 sessions were held in which 184 new employees of central offices were trained on issues concerning sustainability. Training and awareness-raising among employees are key to aligning sustainability policies in all business areas, and for that reason all new employees participate in these sessions, regardless of the role they will have within the organization. Apart from the training activities held at central offices, 181 purchasers were trained at offices during the same year.
Training and capacity building for suppliers
Compliance with the Code of Conduct by suppliers and the application of the Code in their factories is only possible if its contents are known, understood and internalized. Aware of this fact, Inditex upholds an ongoing commitment to training suppliers, placing the resources they need at their disposal.
With a view to continuing to comply with the objective of the Strategic Plan 2014-2018 to include all suppliers in regular training and capacity building programmes, in 2015 substantial resources were invested in providing the appropriate training to the suppliers that require it. Each training activity is specifically designed in line with variables such as the geographic location of the supplier or its experience within the supply chain, while some standard contents are also based on principles that are globally applicable throughout the supply chain. During 2015, a total of 21 training sessions were held with groups of suppliers, while 813 individual training sessions were imparted by the sustainability teams in the range of clusters. A total of 1,300 suppliers received training on sustainability issues. The subjects addressed in training sessions focused mainly on: Inditex’s Code of Conduct; the Compliance Programme, with a special emphasis on Corrective Action Plans; production traceability; sensitivity to gender-equality; and proposals for self-monitoring in the supply chain by suppliers themselves.
Consolidation of the supply chain
Inditex carries out ongoing work to establish lasting relations of mutual trust with its suppliers. Since the Group has a highly consolidated supply chain, it is able to implement activities designed to develop this chain to a more advanced level, responding to specific areas for improvement.
Supplier ratings and their commitment to worker well-being improve in line with the length of their commercial relationship with Inditex. As an example, the top rated suppliers are those that have been part of the Group’s supply chain for longer than three years.
LEAN Project in China
The LEAN Project is an initiative implemented by Inditex’s experts in industrial engineering and promoted by the sustainability team in China. The project’s main aim is to help the factories selected to develop a production management system based on the LEAN philosophy, with a view to improving the working conditions of workers thanks to improved production management systems and increased involvement in the production process.
The LEAN philosophy seeks to optimize processes while valuing the role of the worker, motivating them and ensuring that they continually improve.
This project is implemented in those suppliers and factories that have demonstrated cooperation and transparency in their relations with Inditex. The first phase of the project involves training on basic LEAN concepts and the fundamental role employees play in their introduction. From there, Inditex’s sustainability team collaborates closely with factories on implementing improvements, providing support in the form of guidance throughout the process.
The pilot phase of this project was successful in 2015, involving the participation of two Chinese factories. The improvements made by both factories to their productivity have had a positive effect on employees’ wages. The LEAN Project will continue in 2016, expanding to include more factories and increase the number of workers benefitting from the project.