2. Environmental indicators
This chapter introduces the Inditex system of environmental indicators and the results obtained during 2015. These indicators are a quantitative reflection of the efforts made by the Group to meet our environmental commitments in terms of natural resources, energy resources, waste generation and emissions. The indicators express absolute and relative data based on the number garments released onto the market in the year, in order to demonstrate the innovative environmental management in all areas of business and the efficiency of our activities.
The scope of the indicators includes Inditex’s premises:
- Headquarters and all brand head offices: Zara, Pull&Bear, Massimo Dutti, Bershka, Stradivarius, Oysho, Zara Home, Uterqüe and Tempe, all located in Spain.
- All of the Group’s factories, all located in Spain.
- All of the Group’s logistics centres.
- All of the Group’s own stores and franchises throughout the world.
International offices are not included within this scope. Those indicators for which the scope differs will be described along with the data in question.
To calculate GHG emissions, we follow the recommendations of the Intergovernmental Panel on Climate Change, the IPCC (Guidelines for National Greenhouse Gas Inventories, 2006) and the World Resources Institute GHG Protocol (2015). The emissions factors used are as follows:
- Natural gas: 0.2021 Kg CO2eq/kWh
- Diesel: 2.6853 Kg CO2eq/litre
The emission factors applied to natural gas and diesel are taken from the GHG Protocol tool for calculating emissions derived from stationary combustion v.4.1 by the World Resources Institute (WRI), 2015. Emissions from electricity consumption have been calculated using the emissions factor corresponding to the energy mix of each of the 90 countries in which Inditex operates. The database used corresponds to the GHG Protocol tool for calculating emissions derived from purchased electricity. V. 4.8 (World Resources Institute (WRI), 2015).
Therefore, the conversion factors used to calculate energy consumption are:
- 1 tonne of oil equivalent (toe) = 41.868 GJ
- 103 m3 of natural gas = 0.9315 toe
- 1 tonne diesel = 1.035 toe
- Oil density = 0.832 kg/litre at 15°C (Joint Research Centre, 2007).
Relative indicators are calculated according to the following formula:
Ratio = (absolute value of the year/number of garments released on the market during the year) x 1,000
Garments released on the market*
* Includes all product units released on the market through all the stores, both owned and franchised.
The environmental indicator system includes data collected from 1 February 2015 to 31 January 2016.
Energy consumption
Overall energy consumption of Inditex Group facilities, expressed in terajoules (TJ), comes from the use of fossil fuels (natural gas and diesel) and electricity from the grid. This includes energy consumption in all factories, the head office, branch offices, logistics centres and all of Inditex’s stores worldwide.
The increase in the retail and logistical space over the year have determined the growth of Inditex’s energy consumption, corresponding to 3% in absolute terms with respect to the previous year.. Nevertheless, a remarkable reduction in relative consumption per garment released on the market of 11% is observed, demonstrating the efficiency carried out in the activities of the company.
Overall Energy Consumption (TJ)
A moderate increase in total electricity consumption is observed. However, it is important to note the decrease in relative power consumption, which fell by 11% with respect to the previous year thanks to energy efficiency improvements carried out in our centres. All our facilities are built to meet sustainable architecture criteria and integrate the latest energy management and energy saving technology in their equipment.
Overall electricity consumption (kWh)
Overall consumption of natural gas (toe)
Overall consumption of diesel (toe)
Inditex is firmly committed to renewable energies and their inclusion in the Group’s energy scheme. At Inditex’s various centres, renewable energy facilities such as photovoltaic panels and solar thermal, geothermal and wind generation are combined with trigeneration and cogeneration plants, and air conditioning plants to supply the energy needs of the Group in a more sustainable way. In addition, we integrated the purchase of certified renewable energy at our centres in Spain, in addition to purchases made at stores located in Germany. Thanks to this activity we consumed 224 million kWh of energy from renewable sources, trigeneration and cogeneration, preventing the emission of some 74,799 tonnes of carbon dioxide into the atmosphere.
Consumption of electrical energy originating from renewable sources and co-generation (kWh)
Own logistic centres, own head offices and own factories
Our facilities are built and operated under the criteria of eco-efficiency in order to ensure the efficient and sustainable use of natural resources.
Electricity consumption in own logistic centres, own head offices and own factories
The increase in energy consumption this year is due to the commissioning of our logistics centre located in Cabanillas (Guadalajara, Spain). Thanks to the eco-efficiency measures of the Group, the consumption of electricity per garment released on the market in our logistics centres, own factories and head offices fell by 4% despite the growth in sales and the increase in surface of our facilities. In addition, we initiated a energy efficiency improvement project in our logistics centres that has begun to replace fluorescent lamps with high efficiency LED bulbs, thereby reducing the energy consumption derived from lighting.
Own stores
Since the launch of the Eco-Efficient Store Manual in 2007, more than 2,749 eco-efficient stores worldwide have been built, which, when added to the eco-reforms, means that 54% of Inditex stores are now eco-efficient. Our goal is to reach 100% by 2020. The sustainability and energy efficiency measures of our stores allow relative power consumption to follow a downward trend. In addition, we have increased the number of stores connected to the central platform that controls air-conditioning and electrical plants to monitor generated consumption to 1,444. Thanks to these efforts we reduced relative electricity consumption by 12% compared to 2014.
Estimated electricity consumption in own stores*
* Electricity consumption has been calculated using actual data from the central monitoring platform. To estimate the average consumption data has been considered from 653 stores, with 100% of the same being eco-efficient.
Inditex Greenhouse Gas (GHG) Emissions
The Group’s greenhouse gas (GHG) emissions are calculated and reported in line with the international directives of the Intergovernmental Panel on Climate Change, the IPCC (Guidelines for National Greenhouse Gas Inventories, 2006) and the World Resources Institute (GHG Protocol, 2015). Emissions from electricity consumption have been calculated using the emissions factor corresponding to the energy mix of each of the 90 countries in which Inditex operates. The database used corresponds to the GHG Protocol tool for stationary combustion v. 4.1 (World Resources Institute (WRI), 2015) and GHG Protocol tool from purchased electricity v. 4.8 (World Resources Institute (WRI), 2015). The Inditex Group’s GHG emissions inventory includes direct and indirect emissions for the period February 1, 2015 to January 31, 2016.
A data history based on each of the scopes considered by the GHG Protocol is presented below.
Emissions scopes 1 and 2
- Scope 1: Direct emissions. These are GHG emissions associated with sources under the Inditex Group’s control. It includes:
- Emissions associated with electricity and heat generation in owned premises, detailed at the beginning of the section. Emissions associated with occasional leaks (or isolated leaks) of HFC and PFC gases from air-conditioning equipment are not included.
- Emissions from the use of own vehicles.
- Scope 2: Indirect emissions. Emissions associated with the generation of electricity or thermal energy that Inditex Group buys. The calculation was based on the GHG emissions from all the Group’s facilities, as defined at the beginning of the section. Electricity used in international offices is not included.
2012 | 2013 | 2014 | 2015 | |
---|---|---|---|---|
Scope 1 (t CO2eq) | 24,479 | 22,525 | 21,347 | 22,996 |
Scope 2 (t CO2eq) | 589,758 | 627,982 | 666,188 | 622,879 |
Number of garments released on the market | 869,167,058 | 948,745,988 | 1,018,995,911 | 1,177,784,343 |
g CO2eq per garment released on the market* | 706.70 | 685.65 | 674.72 | 548.38 |
Emissions avoided by using generated thermal energy (t CO2eq) | ND | ND | ND | 5,339.59 |
* The efficiency ratio includes emissions associated with the Group’s operations (scope 1 and 2)
NA: No data available
GHG emissions Scopes 1 and 2
The construction of logistics centres with LEED certification, adequate energy management and process optimization enables us to reduce the GHG emissions per garment by 19%.
Emissions scopes 3
- Scope 3: Optional scope that includes indirect emissions associated with the goods and services supply chain produced outside the organization. Included are emissions from the transport of products from our logistics centres (upstream) and from these to our stores (downstream), both being performed by external logistics operators (air, land and sea transport) as well as the emissions associated with electricity consumption in franchise stores
We calculate the GHG resulting from distribution and logistics operations carried out by external logistics operators based on the vehicles used to transport the product (Scope 3), this year including emissions generated by upstream logistics transport. We must emphasise the reduction in emissions derived from franchised stores, which recorded a decrease of 17% with respect to the previous year.
2012 | 2013 | 2014 | 2015 | |
---|---|---|---|---|
Scope 3 - Downstream transport (t CO2eq) | 398,158 | 462,120 | 596,316 | 672,307 |
Scope 3 - Upstream transport (t COeq) | NA | NA | NA | 428,258 |
Scope 3 - Franchised stores (t CO2eq)* | 100,143 | 108,035 | 113,094 | 94,262 |
NA: No data available
The transport calculation has been carried out based on the weight of the product dispatched and the number of kilometres travelled by each means. The following emission factors, as proposed by the GHG Protocol for mobile combustion V.2.6, are used: (World Resources Institute (WRI), 2015).
- Kg of CO2 /tonne and km truck (load over 33 t)= 0.08678
- Kg of CH4/tonne and km truck (load over 33 t)= 2.3973*10-6
- Kg of N2O /tonne and km truck (load over 33 t)= 1.8494*10-6
- Kg of CO2 /tonne and km short haul flight (< 463 Km)= 1.96073
- Kg of CH4/tonne and km short haul flight (< 463 Km)= 2.8562*10-5
- Kg of N2O /tonne and km short haul flight (< 463 Km)= 3.2809*10-5
- Kg of CO2 /tonne and km medium haul flight (between 463 and 1108 Km)= 1.47389
- Kg of CH4/tonne and km medium haul flight (between 463 and 1108 Km)= 2.8562*10-5
- Kg of N2O /tonne and km medium haul flight (between 463 and 1108 Km)= 3.2809*10-5
- Kg of CO2 /tonne and km long haul flight (> 1108 Km)= 0.61324
- Kg of CH4/tonne and km long haul flight (> 1108 Km)= 2.8562*10-5
- Kg of N2O /tonne and km long haul flight (> 1108 Km)= 3.2809*10-5
- Kg of CO2 /tonne and km ship= 0.0079
- Kg of CH4/tonne and km ship= 2.8083*10-6
- Kg of N2O /tonne and km ship= 9.5892*10-7
Inditex, zero waste to landfill
At Inditex we have the goal that before 2020 none of the waste from our activities will end up in landfill. To achieve this, we continue, with the effort and commitment of all our employees, to improve the source separation processes. In addition, we have the Waste Minimization Plan which, as with other projects such as Green to Pack or Closing the Loop, allows action to be taken the length of our value chain to continue progressing towards our objective. The waste generation data below refers to the waste generated in head offices, brand head offices, all Inditex factories and logistics centres. It does not include the waste generated in stores.
Evolution of recovered products to send to recycling (kg)
All waste generated by Inditex is collected and managed by a legally authorized body that sends the waste for recycling (in the case of paper and cardboard, plastic, metal, textile remains, among others), and other appropriate treatments which allow it to be recovered. In 2015, more than 85% of our waste was managed in a way that does not harm the environment.
Green to Pack and reusable systems
Thanks to the launch of the Green Pack programme, we work with our suppliers to optimize the packaging used throughout the supply chain. Using homogenization measures and standardized packaging we favour reuse and improve separation and recycling of this waste. In 2015, we started reuse systems for boxes, tubes, pallets and bags which are added to the alarm and reusable hanger systems already implemented. This year alone, these systems have allowed 815 million alarms and 87 million plastic hangers to be recycled. These measures, in addition to the cost saving, represent an important environmental benefit because reusing avoids the consumption of natural resources and the atmospheric emissions associated with their manufacture and recycling.
Closing the Loop
Thanks to the Closing the Loop project, we collaborate with social organizations, universities and leading companies in the sector to obtain efficient solutions for recycling textile waste from manufactured and used garments that are not reusable, creating new raw materials whenever possible of equal or higher quality than those collected, allowing the closure of the production cycle.
Products recovered to be sent for recycling (kg)
Annual generation of urban waste or similar
This waste is classified in accordance with the European Waste Catalogue (EWC) and its transposition into national and regional legislation. Waste cardboard and paper, textile, plastic, wood and metal are managed by a legally authorized body that sends the waste for recycling. The increase in the generation of these wastes is due to the expansion of the logistics capacity of the Group, as well as the maintenance of the current capacity and improvement in source separation processes.
Absolute data (kg)
Improvements in source separation processes during 2015 have allowed the Group to establish the amount of recycled metals, as well as part of the textile waste. Thanks to the Closing the Loop project, textile waste is also properly managed for recycling, while previously this was included in the urban waste category.
Evolution of principal hazardous waste
This year we continue to improve the tasks of source separation and the subsequent shipment to authorized agents, promoting the recycling of hazardous wastes or other appropriate treatment which allows proper recovery and environmental management. In this way, in 2015 we managed to recycle 89% of this type of waste. Peaks are observed in waste generation such as with fluorescents or batteries due to replacement by more efficient equipment such as lamps with LED technology and lithium-ion batteries, actions which are undertaken under the logistics centres efficiency improvement project.
Type of waste (kg) | Final treatment | 2012 | 2013 | 2014 | 2015 |
---|---|---|---|---|---|
Batteries | Recycling | 3,191 | 2,929 | 5,597 | 9,532 |
Electronic waste | Recycling | 4,251 | 6,673 | 6,901 | 10,094 |
Fluorescents | Gas extraction and recycling | 767 | 2,827 | 3,183 | 5,387 |
Oil filters | Recycling | 435 | 671 | 500 | 761 |
Contaminated metal containers | Recycling | 413 | 530 | 865 | 2,284 |
Used mineral oil | Recycling | 6,629 | 4,432 | 8,302 | 15,080 |
Contaminated absorbents | Energy recovery | 2,501 | 3,259 | 4,262 | 2,786 |
Paint | Recycling | 106 | 554 | 1,020 | 465 |
Contaminated plastic containers | Recycling | 1,080 | 1,648 | 1,578 | 1,366 |
Destination of waste according to type and treatment
As part of the final stage of Inditex’s Waste Minimization Plan, all waste generated by the company is collected and managed by a legally authorized body that sends the waste (principally paper and cardboard, wood, plastic, metal, textile remains) for recycling or other appropriate treatment which allows proper recovery and environmental management.
Proportion of waste generated by weight
The packaging materials released on the market (paper and plastic bags, labels, protective elements) along with the products sold by Inditex are adequately managed by authorized bodies. Inditex subscribes to the Integrated Management Systems for Packaging and Wrapping available in countries that employ them. The company’s commitment to these systems means that each Inditex brand pays a non-profit management agency to collect and manage the waste generated by the stores. This management agency is established with the recognition of the authorities of each country (Ecoembes in Spain) to ensure that the waste generated by stores is collected, managed and recycled correctly.
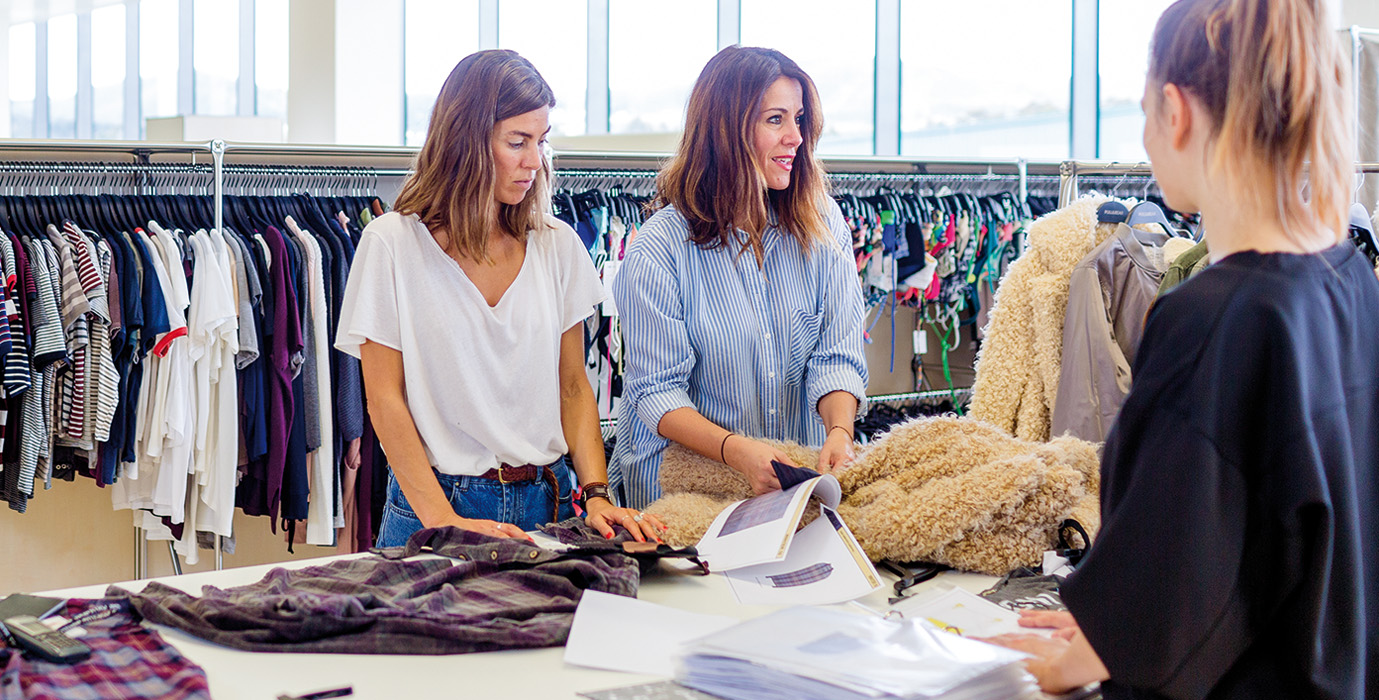
In terms of the recovery of products released on the market, it is not viable to assess the volume generated nor its management on a worldwide level, given that there is no specific collection or management system for textile materials on a global level.
Water consumption in own offices, Inditex own factories, own logistics centres and own stores
Data on water consumption comes from direct measurements and supplier bills (public supply networks) from offices, all Inditex’s factories, logistics centres and own stores.
Despite the increase in water consumption compared to previous years due to the growth in logistics capacity and store openings, we continue to reduce the relative consumption, highlighting the efficiency of our facilities in reducing this resource.
Water consumption in head offices, Inditex factories, logistics centres and own stores (m3)
Water supplied to all the centres for use both in processes and for consumption comes from public, authorised supply networks. Inditex has no impact on protected habitats.
The greatest water consumption is by domestic use, fundamentally cleaning and sanitation, guaranteeing its discharge to municipal sewage systems.
In the area of industrial activities, water is mainly required for steam generation and industrial refrigeration in a closed cycle, where recirculation systems are used. Discharge of waste water from all installations is carried out via sanitation networks, in all cases with the corresponding administrative authorization. This requires periodic analyses to guarantee compliance with the law in force. The amount of waste water can be calculated as equal to water consumed, as there are no productive processes that consume water and the cooling systems use a closed cycle.