2. Assessment of the supply chain
Assessments and analysis provide knowledge of the type of supply chain Inditex has at its disposal, as well as its strengths and areas for improvement.
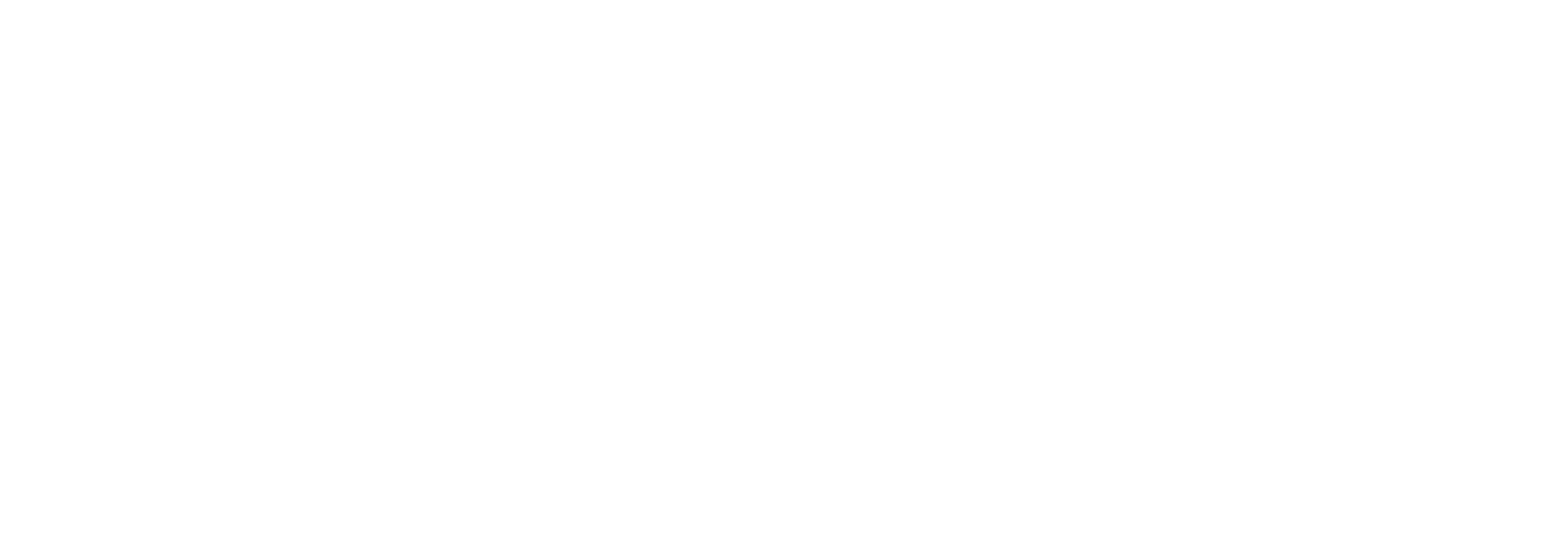
Compliance programme
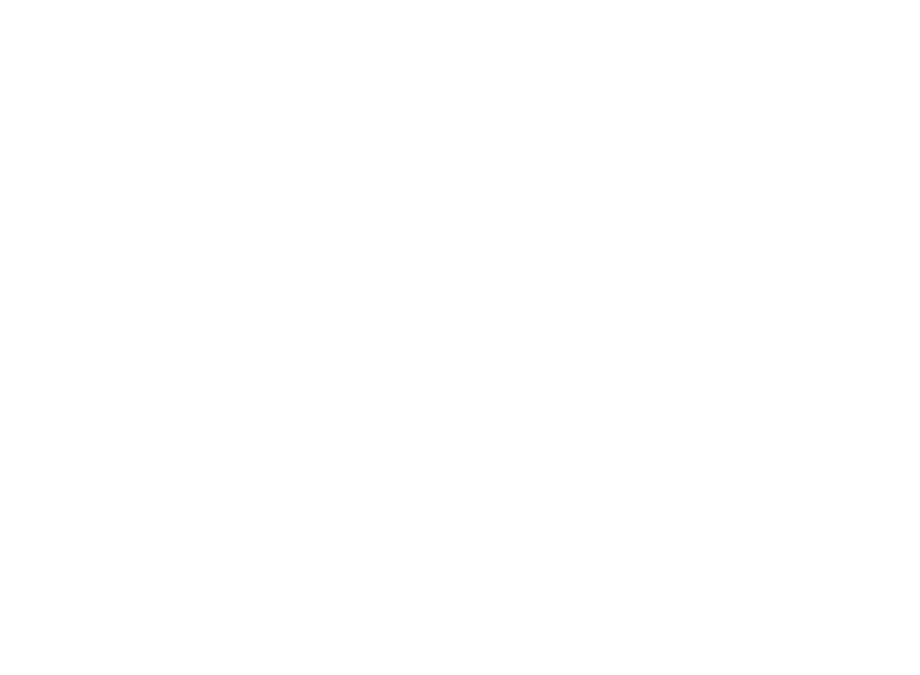
The Compliance Programme ensures that all suppliers of the Inditex Group observe the Manufacturer and Supplier Code of Conduct. The programme employs different assessment tools that allow full analyses to be made of the supply chain, identifying its strengths and needs.
As a result of social audits, each supplier receives a rating which is modified according to their level of compliance with the Code of Conduct. Based on the results of social audits, and analysing compliance in each aspect of the Code of Conduct, areas for improvement are identified and programmes and plans are developed that focus on improving workers’ conditions, and compliance with environmental and product health and safety standards.
Inditex’s objective is for 100% of its suppliers to be classified as grade A or B by 2018, which would represent a high level of compliance with the Code of Conduct. In 2014, some 85% of suppliers with purchase were classified as grade A or B. These 1,377 suppliers are responsible for 93% of Inditex’s production, over the ratios achieved in previous years.
Suppliers with purchase in 2014
2014 | 2013 | |||
---|---|---|---|---|
Supplier classification* | Suppliers | % Suppliers | Suppliers | % Suppliers |
A | 678 | 42% | 697 | 44% |
B | 699 | 43% | 614 | 39% |
C | 133 | 8% | 128 | 8% |
CAP | 54 | 3% | 82 | 5% |
PR | 61 | 4% | 71 | 4% |
Overall total | 1,625 | 100% | 1,592 | 100% |
*Supplier A: complies with the Code of Conduct
Supplier B: fails to comply with a non-material aspect of the Code of Conduct
Supplier C: breaches a sensitive aspect of the Code of Conduct
Supplier subject to corrective action: suppliers that breach critical aspects of the Code of Conduct are immediately brought under a corrective action plan
Supplier PR: Undergoing the auditing process
Compliance with each of the different sections of the Code of Conduct is analysed to identify areas for improvement and establish specific programmes.
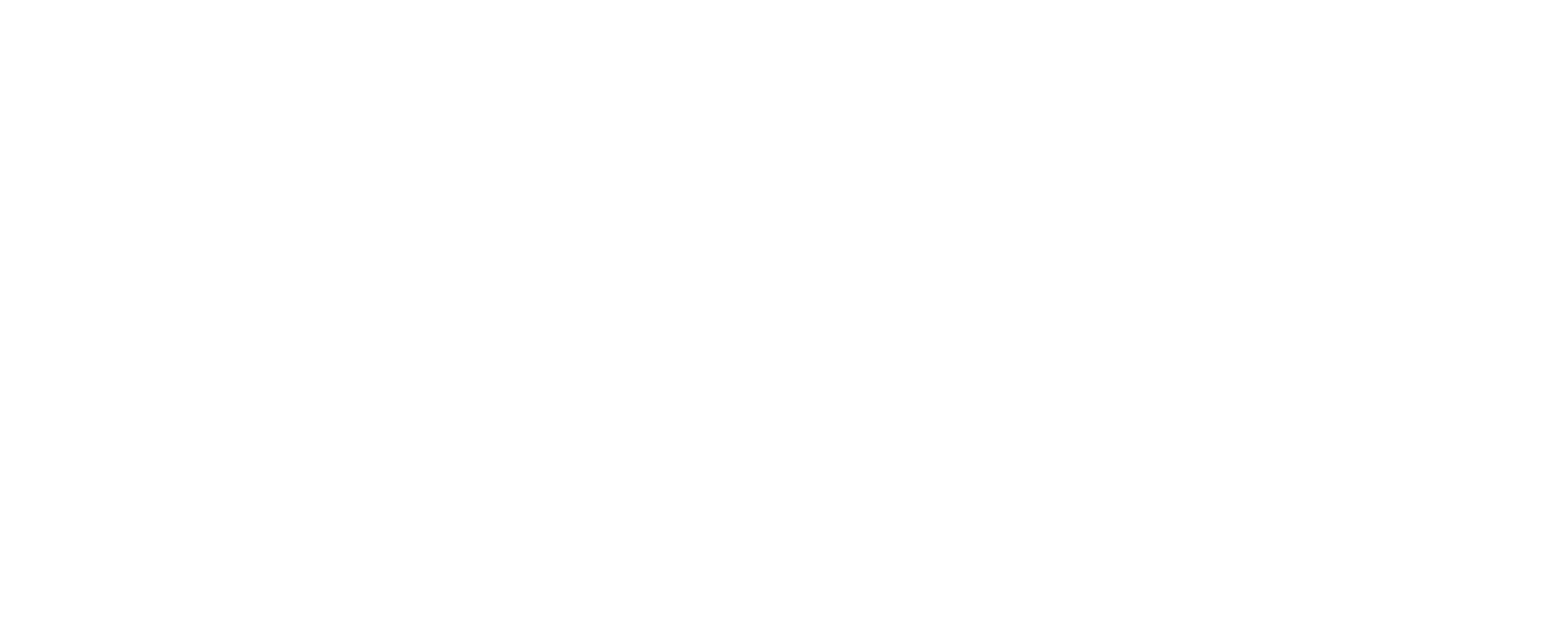
*Does not include the factories rejected in 2014.
**Includes the lack of suitable systems for checking the age of workers.
***Includes the lack of suitable systems for registering and informing workers.
Promotion of education
Inditex has developed specific programmes to cover critical areas in the case of breaches of the Code of Conduct. One example of this is the programme From Production back to Education.
In collaboration with non-profit organizations such as the Association for the Support of Contemporary Living (CYDD) in Turkey; Pratham, India; and Awaj, Bangladesh, Inditex’s Plan for the Prevention and Remedy of Child Labour seeks to protect and guarantee the rights of minors, in particular their right to education, regardless of their family financial situation. Consequently, when a situation of child labour is identified, the supplier is considered to be responsible for ensuring the education of the minor, assuming the costs deriving from their education until they reach the legal working age. At that time, the worker will have the opportunity to take up their previous job once more if they wish. During the time that the minor forms part of the Remedy Plan the supplier must pay a sum equivalent to the wages payable to the minor or hire another member of their family of legal working age. Moreover, the factory and the supplier must develop and implement measures to avoid future cases of child labour, thereby contributing to eradicating such practices.
In this way, Inditex pay special attention to guaranteeing and protecting the rights of minors in all communities where it operates, with a particular focus on promoting the right to education.
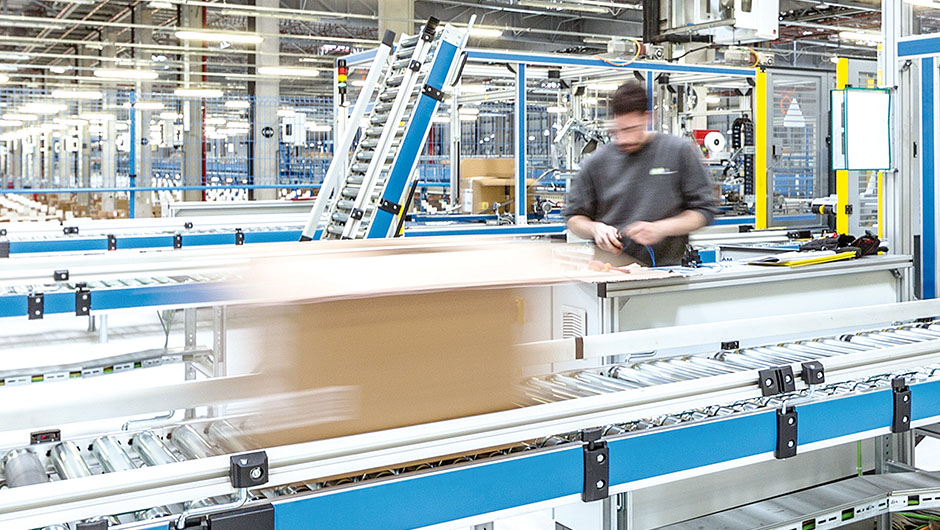
Worker participation
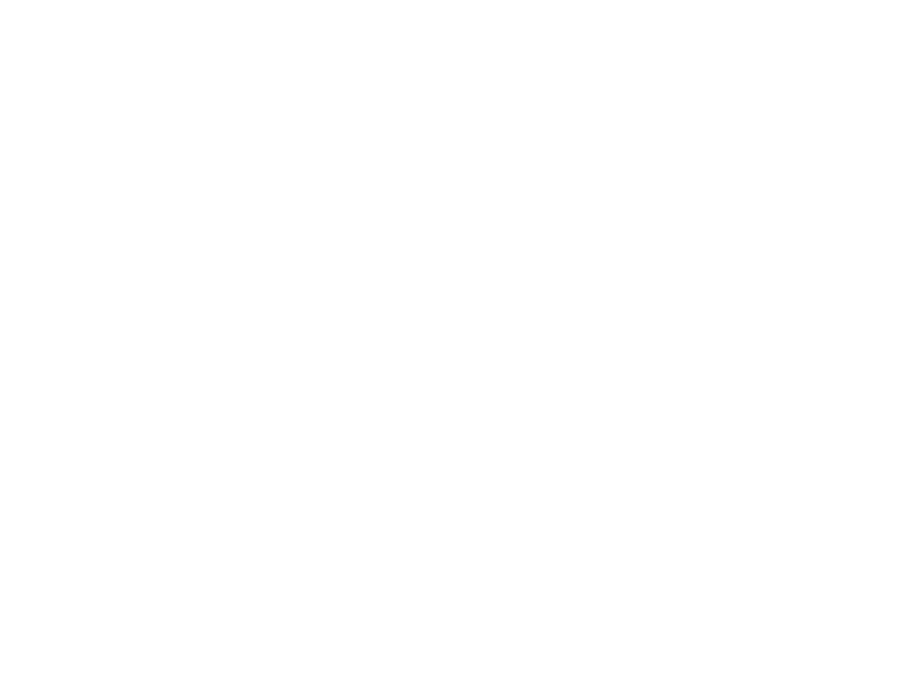
Inditex firmly believes that the party best able to protect worker rights are the workers themselves. That's why it is essential that workers know their rights, establish fruitful dialogue, and have the collective bargaining mechanisms they need to safeguard those rights.
The work of trade unions is one of these mechanisms, and collaboration with the international trade union federation IndustriALL and local trade unions by means of the Framework Agreement signed in 2007 is essential to establishing and promoting initiatives to provide information and increase worker autonomy. The Framework Agreements were renewed in 2014.
In 2014, the Framework Agreement with IndustriALL has been implemented in the following activities:
- Transparency of the supply chain: Inditex shares all information on its supply chain, which is updated on a regular basis, with IndustriALL.
- Promotion of initiatives favouring decent wages in the supply chain based on improved conditions for worker dialogue and negotiation.
- Implementation of the Framework Agreement on a local level throughout Inditex’s supply chain, as established in the protocol signed by Inditex and IndustriALL in 2012, which develops the Framework Agreement:
- Training programme in Turkey in collaboration with the Istanbul Ready-Made Garments Exporters' Associations (IHKIB), the local trade union Öziplik-i and the Kocaeli University of Istanbul. The project began in 2013 as a pilot project, and has continued to be developed with activities following up on the training carried out in the previous year. The experience has been repeated in a factory where 30 employees received training and mechanisms were established for the free election of representatives.
- Joint Turkey Programme: Within the framework of this programme in collaboration with IndustriALL and other international brands to improve working conditions and labour relations, in 2014 training was imparted to 116 workers’ representatives, supervisors and management in the rights and duties of workers and communication and negotiation. The training was imparted by academics from the Kocaeli University of Istanbul.
- Analysis of the textile industry in Tunisia with the aim of getting to know the real situation of the sector in the country, establishing relations with local trade unions and designing future actions to meet worker needs.
- Joint interventions with IndustriALL representatives, local trade unions and supplier and employer representatives in a range of countries, as Indonesia and Portugal, for conflict resolution.
- Collaboration with the communications department of IndustriALL to raise awareness in the textile industry in countries such as Turkey and Bangladesh, and the positive effects of the Framework Agreement.
Decent wages
Living wages is a concept considered by the International Labour Organization to be one of the fundamental human rights required to achieve “universal and lasting peace”, as established in the text of the ILO Constitution of 1919.
The concept and implementation of a living wage lacks an standardized definition or measurement, although in recent years some important progress has been made to guarantee that workers in the supply chain are paid wages that are sufficient to cover at least the basic needs and any other that might be considered reasonable additional needs of the workers and their families, as set out in Inditex’s Code of Conduct.
In collaboration with its stakeholders, Inditex implements various programmes that aim to guarantee that living wages are paid to workers in its supply chain. These programmes mainly involve capacity building for workers to allow collective bargaining to take place with the participation of all the required stakeholders to ensure effective social dialogue. A result of this has been the implementation of the following working lines:
Promotion of collective bargaining
By means of the Framework Agreement signed with IndustriALL in 2007, Inditex has implemented various programmes within its supplier clusters to promote collective bargaining through freely chosen worker representatives. Since then, programmes have been carried out in countries such as Portugal, Morocco, Turkey, Argentina, Brazil, Tunisia and China.
Inditex shares the list of suppliers and factories with IndustriALL on a regular basis, as well as with local trade unions, in order to facilitate the correct implementation of these programmes.
Improving production systems
Inditex creates value through projects to improve productivity and efficiency in factories, with a view to achieving better payment for workers employed in these factories. In this way, Inditex in collaboration with IndustriALL has implemented pilot projects in Turkey that have demonstrated that it is possible to achieve wage improvements without increased costs for suppliers or for clients.
Improvements to factors such as production systems, human resources management and safety and factories are the objectives of the programme implemented with the assistance of the ILO in China. To date, the programme has been implemented in two factories with very encouraging results that it is hoped can be extended to other factories as of 2015.
Responsible purchasing practices
Inditex’s CSR teams impart regular training sessions for purchasers with the aim of raising their awareness of how their purchasing decisions influence the factories used. A better knowledge of the supply chain, provided by the internal tool for Order Management, encourages more efficient purchasing and avoids the breaches that can occur due to incorrect planning.
Specifically, in 2015, Inditex will carry out purchase training programmes employing the Ethical Trading Initiative (ETI) Methodology for purchasing practices, which it is expected to be implemented, both in the company’s purchasing teams in Spain and teams in other countries.
Collaboration with stakeholders
Collaboration with different stakeholders is fundamental to achieving decent wages for workers in Inditex’s supply chain, allowing them to cover their needs and have at their disposal a discretionary income.
To this end, in 2014 in conjunction with other international brands, Inditex signed the Enabling Principles that form the basis of a way of working to achieve decent wages in supply chains. Based on the various meetings being held with the assistance of other stakeholders, we expect to implement projects that position the textile industry as a benchmark for other sectors in issues of social dialogue with the necessary assistance of governments, trade unions, employers' organizations and NGOs, among other actors.
Wage increases in Cambodia
For Inditex, assuring a decent wage for all workers is one of the pillars of the management of its supply chain. This is why Inditex has always been an active promoter of social dialogue between all parties involved, based on experience that collective bargaining is the most effective way of achieving sustainable measures adapted to the real needs of workers.
Based on these principles, Inditex, in collaboration with other brands and the international trade union IndustriALL issued a letter to the government of Cambodia and the employers' association, Garment Manufacturers Association in Cambodia (GMAC) on 18 September 2014, urging them to engage in negotiations on wage increases with the participation of all parties, the government, employers’ organization and workers’ representatives.
As a result of negotiations between the parties, on 12 November 2014 the Government of Cambodia announced a new minimum wage of 128 dollars per month for the sector of clothing and footwear manufacturing industry for 2015, which constitutes an increase of 28%. This is an achievement which, thanks to technical support from the ILO and the agreement reached between trade unions, employers and the Government, aims to guarantee that all workers enjoy a minimum standard of living compatible with a dignified existence, as set out in Cambodia’s Employment Law.
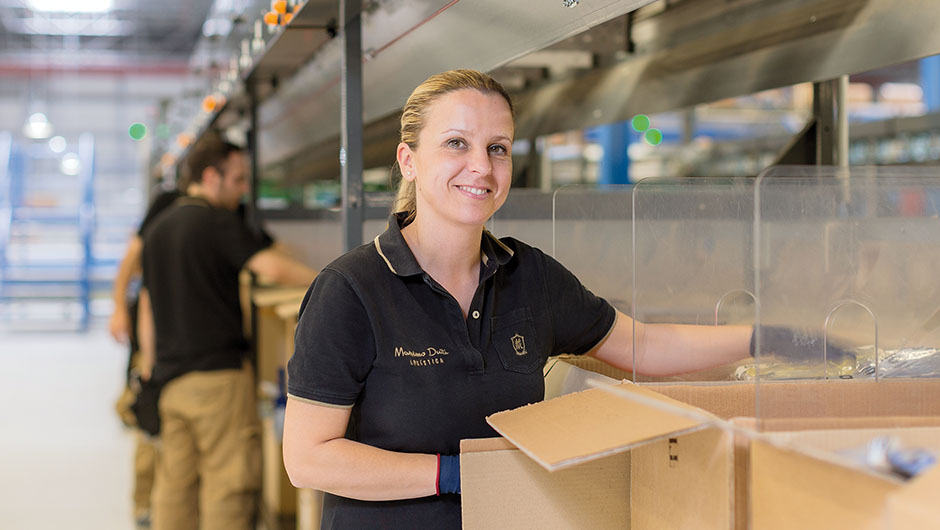
Corrective action plans
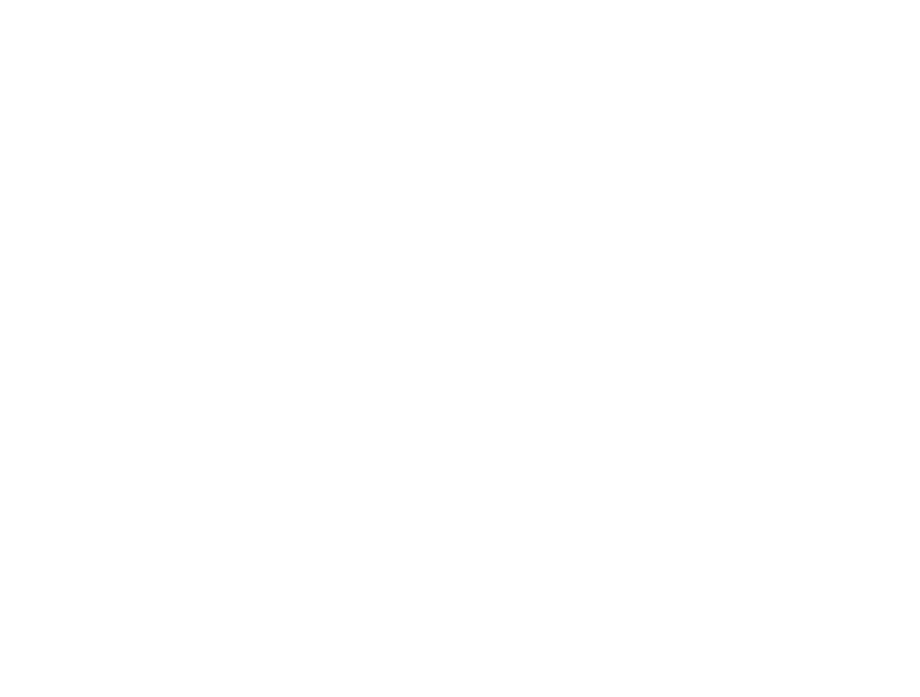
After every audit, Inditex establishes Corrective Action Plans and supports and advises each factory on their application. Other entities such as trade unions and NGOs may also take part in this process. These plans are particularly strict in the case of factories that have committed certain breaches of the Code of Conduct (Project D). In such cases, plans are established for up to six months and are supervised by Inditex teams on the ground.
Corrective Action Plans 2014 (Project D)
Geographic area | Factories that initiated an improvement process | Factories that improved their compliance | Factories in the process of improvement | Percentage of CAPS successfully completed |
---|---|---|---|---|
Africa | 19 | 10 | 7 | 83% |
America | 2 | 2 | 0 | 100% |
Asia | 336 | 174 | 87 | 70% |
Europe (non-EU) | 155 | 27 | 67 | 31% |
European Union | 52 | 14 | 18 | 41% |
Total | 564 | 227 | 179 | 59% |
Since continual improvement is one of the primary goals of supply chain management, Inditex exercises zero tolerance with those who do not take advantage of the opportunities given to them to ensure compliance with the standards set out in the Code of Conduct and local legislation. Factories that did not manage to meet the requirements of a Corrective Action Plan in 2014 have been rejected, and cannot form part of Inditex’s supply chain.
In 2014, some 56 suppliers were rejected due to breaches of one or more of the requirements and principles that must be complied in order to work with Inditex, including 30 suppliers that breached the Code of Conduct.
Active suppliers on 31 January 2015
Geographic area | Suppliers with purchase * | Rejected due to a breach of the Code of Conduct | Rejected for commercial reasons | Active suppliers at 31/01/2015 |
---|---|---|---|---|
Africa | 135 | 2 | 2 | 131 |
America | 80 | 5 | 7 | 68 |
Asia | 759 | 13 | 10 | 736 |
Europe (non-EU) | 160 | 5 | 1 | 154 |
European Union | 491 | 5 | 6 | 480 |
Total | 1,625 | 30 | 26 | 1,569 |
(*) Suppliers of fashion items, mainly clothing, footwear and accessories, with a production of over 20,000 units/year. Suppliers with smaller production account for 0.43% of total production.
Competence visits
Each of the Corrective Action Plans is developed on an individual basis and is personalized. The development of plans is coordinated between the supplier, the factory, Inditex’s teams and, where necessary, other stakeholders. This joint initiative has a shared objective: to improve working conditions and the working environment of employees in the factories that form part of Inditex’s supply chain. Part of this monitoring work takes the form of competence visits to evaluate the measures put in place. In 2014, Inditex’s CSR teams on the ground performed a total of 1,190 competence visits.