5. Sustainability of the supply chain
The ultimate goal of Inditex’s Strategic Plan for a stable and sustainable supply chain 2014-2018 is to achieve sustainability understood in terms of both time and social aspects.
All the policies, programmes and activities set out in the sections on identification, assessment and optimization have the final goal of ensuring sustainability in the supply chain and compliance with the principles of the Ruggie Framework (see page 43). Inditex has 10 supplier clusters in the geographic areas where it has a larger and stronger presence: Spain, Portugal, Morocco, Turkey, India, South East Asia, Bangladesh, China, Brazil and Argentina. In 2014, the production of suppliers located in the various clusters accounted for 91% of total production.
Further information at www.inditex.com/en/sustainability/suppliers/working_in_clusters
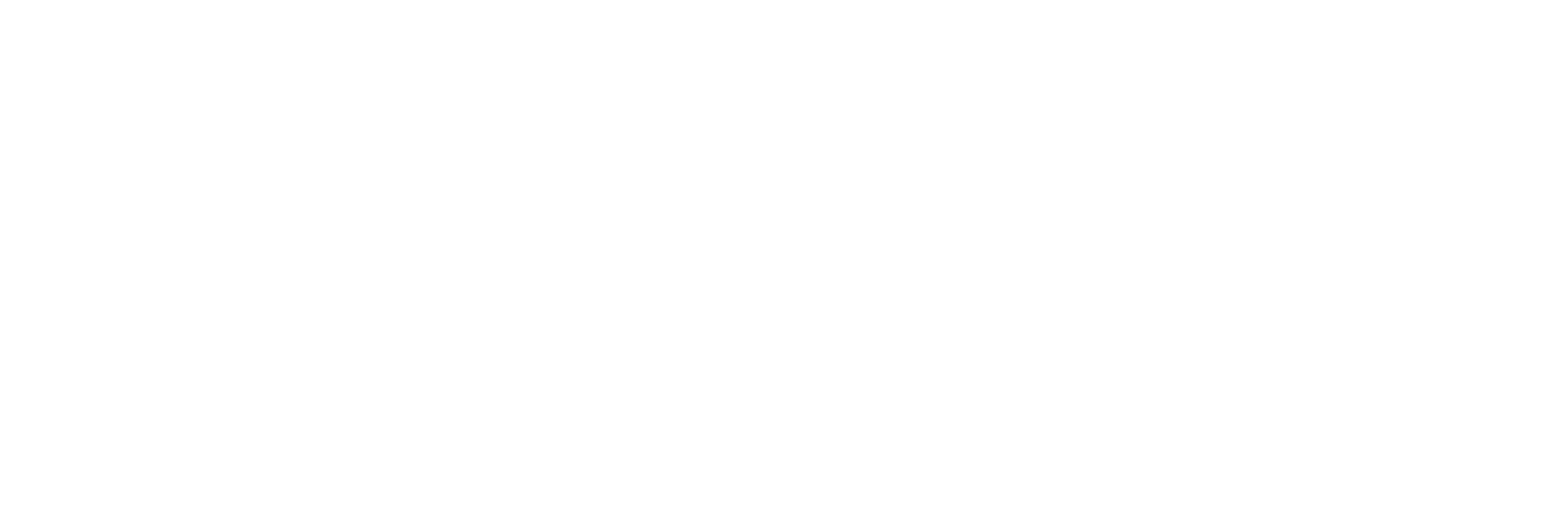
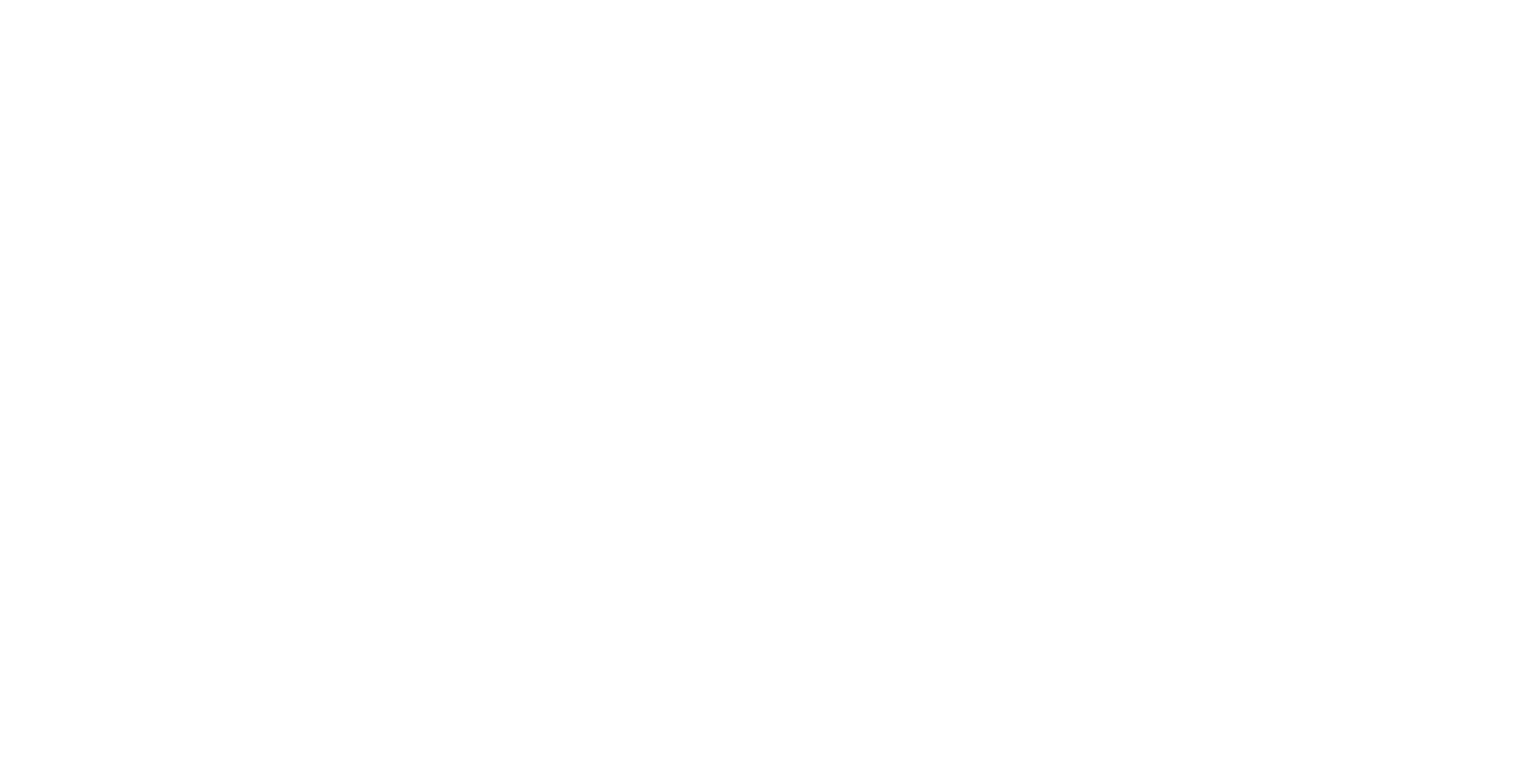
Cluster | Spain | Portugal | Morocco | Turkey | India | Bangladesh | South East Asia | China | Brazil | Argentina |
---|---|---|---|---|---|---|---|---|---|---|
Internal team | 12 | 2 | 2 | 6 | 6 | 7 | 1 | 8 | 1 | 1 |
External team | 26 | 36 | 10 | 32 | 45 | 25 | 48 | 412 | 51 | 16 |
![]() |
![]() |
![]() |
![]() |
![]() |
|
---|---|---|---|---|---|
Spain | Portugal | Morocco | Turkey | India | |
IDENTIFICATION | |||||
Traceability | - | - | 163 production audits | 57 production audits | 152 production audits |
Coordination with purchasing teams in the different brands, local CSR teams and suppliers to ensure traceability throughout the supply chain | In 2014, design of a Production Control programme based on analysis of information and production monitoring visits to be implemented in 2015 | The information provided by the supplier is compared with the factories’ capacities, while regular monitoring visits are also performed | Production monitoring is performed not only by means of production audits but also during each social audit or factory visit. Orders are analysed and compared with the relevant documents on the factory’s production | The production monitoring process begins with an analysis of orders and processes along with a preliminary analysis of the factory’s capacity. Monitoring measures are also applied to raw materials and all the components required to finish production | |
Training for auditors | 13 auditors trained | 39 auditors trained | 7 auditors trained | 85 auditors trained | 78 auditors trained |
Various sessions were held on the launch of the new methodology for audits | Apart from the training sessions imparted to new auditors, training sessions were held with the aim of standardizing and improving the audit process | Specific training for occupational health and safety auditors (relevant legislation, monitoring of health and safety systems, best practices in risk assessment) | One of the aspects focused on by the cluster in the training given in 2014 is improving the quality of initial audits | Of the nine sessions held in 2014, five had the aim of training auditors in the performance of pre-assessment audits. The four remaining sessions focused on the performance and improvement of the social audit process | |
Audit quality management | |||||
Pre-assessment audits | 64 | 305 | 45 | 436 | 125 |
Social audits | 64 | 701 | 105 | 730 | 308 |
Special audits | - | 33 | 462 | 24 | 404 |
ASSESSMENT | |||||
Compliance programme | |||||
Suppliers A: | 103 | 115 | 55 | 65 | 69 |
Suppliers B | 80 | 29 | 42 | 68 | 41 |
Suppliers C | 11 | 5 | 7 | 14 | 11 |
Suppliers CAP | 5 | 5 | 10 | 10 | 5 |
Worker participation | Coordination of the global implementation of the Framework Agreement with IndustriALL Global Union and all activities developing the Agreement in the different clusters | Collaboration and ongoing dialogue with the Portuguese trade union FESETE to promote worker rights in the country’s textile industry | Visits to manufacturers in the Inditex’s supply chain with the aim of performing and analyses of the textile industry in Tunisia, establishing relations with local trade unions and designing future actions to meet worker needs | Joint Turkey Programme: Collaborative programme with IndustriALL and other international brands to improve working conditions and labour relations: in 2014, training was imparted to 116 workers’ representatives, supervisors and management in the rights and duties of workers and communication and negotiation | Completion of the pilot programme in collaboration with St. John’s Medical College to protect the hygiene, nutrition and health of workers based on training and participation of employees to ensure their welfare. The programme will continue to be implemented in 2015 |
Corrective Action Plans | n/a | 41% success rate | 82% success rate | 31% success rate | 84% success rate |
Sharing good practices | Representation of Inditex in international platforms such as the Ethical Trading Initiative, UN Global Compact, ILO, or participation in the Better Work Global Buyers’ Forum, in which international brands collaborate to achieve progress on sustainability issues | Collaboration with the Catholic University of Portugal, Porto, to train young social auditors | Launch of a programme in collaboration with Medicus Mundi to provide care for the health and safety of workers in the supply chain | Collaboration with the NGO Refugee Support Centre to address the working conditions of immigrant workers, establishing corrective plans, including requesting work permits and the development of training programmes tailored to worker needs | "Sowbhagyam” programme against worker exploitation in the south of India in collaboration with the NGO SAVE with the aim of raising awareness in the community of the prevention and abolition of the sumangali system in the textile industry. To date, more than 26,806 young people have benefited from the programme, which has covered 136 towns and 231 schools |
OPTIMIZATION | |||||
Effective auditing | 187 new employees in Inditex Spain trained in CSR | Coordination with purchasing teams by means of the Spain cluster | Communication of the results of audits and the development of Corrective Action Plans to purchasing teams | Six training sessions for local purchasers in CSR issues | Four training sessions on traceability and other sustainability practices for local purchasers with a total of 41 participants |
Training and capacity building for suppliers | Daily management of supplier capacity building and coordination with training activities held in clusters | 27 suppliers trained | 24 suppliers trained | 77 suppliers trained | 368 suppliers trained |
![]() |
![]() |
![]() |
![]() |
![]() |
|
---|---|---|---|---|---|
Bangladesh | South East Asia | China | Brazil | Argentina | |
IDENTIFICATION | |||||
Traceability | 60 production audits | 123 production audits | 153 production audits | 1,313 production audits | 438 production audits |
During the year 2014, 60 production audits were performed in order to ensure production traceability in the country. “Chalanes”, documents recording deliveries and dispatches of merchandise are analysed and compared for each factory | The method used in production audits includes the analysis of information concerning Inditex orders, which is compared with the factory’s documentation and real production | Traceability monitoring in China is performed in all visits and audits. Moreover, the specific production audits performed – 153 in 2014 – allow the analysis of the capacity of factories and the identification of areas for improvement | 100% of orders in Brazil are monitored every two weeks, ensuring sufficient monitoring of all phases of production for every order | The auditor checks where garments are manufactured according to the sample of orders contained in the audit request. In order to document the process, the auditor produces a report, order by order, attaching documents that support their conclusions. | |
Training for auditors | 26 auditors trained | 27 auditors trained | 53 auditors trained | 3 auditors trained | 30 auditors trained |
The cluster held two training sessions to strengthen the methodology used for the pre-assessment audits performed for all production processes | Training for auditors; shadow audits were also performed in which a member of Inditex’s team accompanied the external auditor to observe and assess their performance | During the year 2014 training sessions involving external auditors were held to train new auditors | The cluster combined training targeted at auditors working for external companies with training for the Group’s internal team | In line with the objective of developing a comprehensive production traceability process, and in collaboration with the National Industrial Technology Institute (INTI), the cluster held training sessions on various production techniques key to detecting cases of order diversion | |
Audit quality management | |||||
Pre-assessment audits | 96 | 102 | 810 | 88 | 50 |
Social audits | 310 | 163 | 870 | 248 | 140 |
Special audits | 324 | 176 | 126 | - | 2 |
ASSESSMENT | |||||
Compliance programme | |||||
Suppliers A | 23 | 2 | 47 | 23 | 30 |
Suppliers B | 57 | 5 | 191 | 1 | 2 |
Suppliers C | - | 1 | 52 | 1 | - |
Suppliers CAP | 3 | 1 | 7 | - | - |
Worker participation | Collaboration with the communications department of IndustriALL to raise awareness of the textile industry, the positive effects of the Framework Agreement and joint work on the implementation of the Accord | Representation and presence of international and local trade union representatives in meetings and training for suppliers in the region | Development and implementation of the first three modules of the International Labour Organization’s SCORE programme in two factories. The programme aims to combine the efforts of employees, management and trade unions to improve productivity in factories | Regular collaboration with the National trade union CONACCOVEST ( Conferação Nacional dos Trabalhadores nas Indústrias do setor Textil, Vestuário, Couro e Calçados) to improve social conditions by means of increased productivity | Identification and adjustment of job categories to the corresponding trade union, guaranteeing improved remuneration for employees and greater control for factories |
Corrective Action Plans | 79% success rate | 62% success rate | 63% success rate | 100% success rate | n/a |
Sharing good practices | Active participation as a member of the Steering Committee of the Accord on Fire and Building Safety in Bangladesh and ongoing collaboration with the Bangladesh Garment Manufacturers and Exporters Association (BGMEA) and other entities representing the sector | Collaboration with the ILO Better Work programmes with more than 30 factories registered to the Better Factories Cambodia programme and four factories registered with the ILO Better Work Vietnam programme to protect human rights | Active participation in meetings of the China Caucus of the Ethical Trading Initiative in 2014 to deal with the challenges faced by the industry and share good practices, seeking joint solutions | Support for the social organizations Centre for Human Rights and Immigrant Citizenship (Centro de Direitos Humanos e Ciudadania do Imigrante, CDHIC), the Migrant Support Centre (Centro de Apoio ao Migrante, CAMI) and MISSÃO PAZ, reiterating Inditex’s commitment to promoting human rights and improving employment and social conditions within its supply chain. Some 17,524 immigrants in a situation of social risk have benefitted directly from this initiative | Collaboration with the National Industrial Technology Institute (INTI) to develop competencies in aspects of production and improve the efficiency of audits by means of the inventory of processes |
OPTIMIZATION | |||||
Effective auditing | Regular training for 14 local purchasers on purchasing practices and supply chain management | Ongoing monitoring by purchasing teams of the working conditions of employees | 14 meetings with local purchasers on traceability and Corrective Action Plans | Coordination of CSR activities with all business areas | 18 meetings with local purchasers to deal with specific themes related to supply chain management |
Training and capacity building for suppliers | 371 suppliers trained | 16 suppliers trained | 240 suppliers trained | 27 suppliers trained | 21 suppliers trained |