3. Optimization of the-supply chain
Inditex understands that it must help its suppliers to improve their production conditions and support them in this process throughout their commercial relationship with the ultimate goal of ensuring the sustainability of the-supply chain. To this end, various initiatives and projects are implemented with the aim of improving auditing processes, training suppliers and consolidating a stable supply chain.
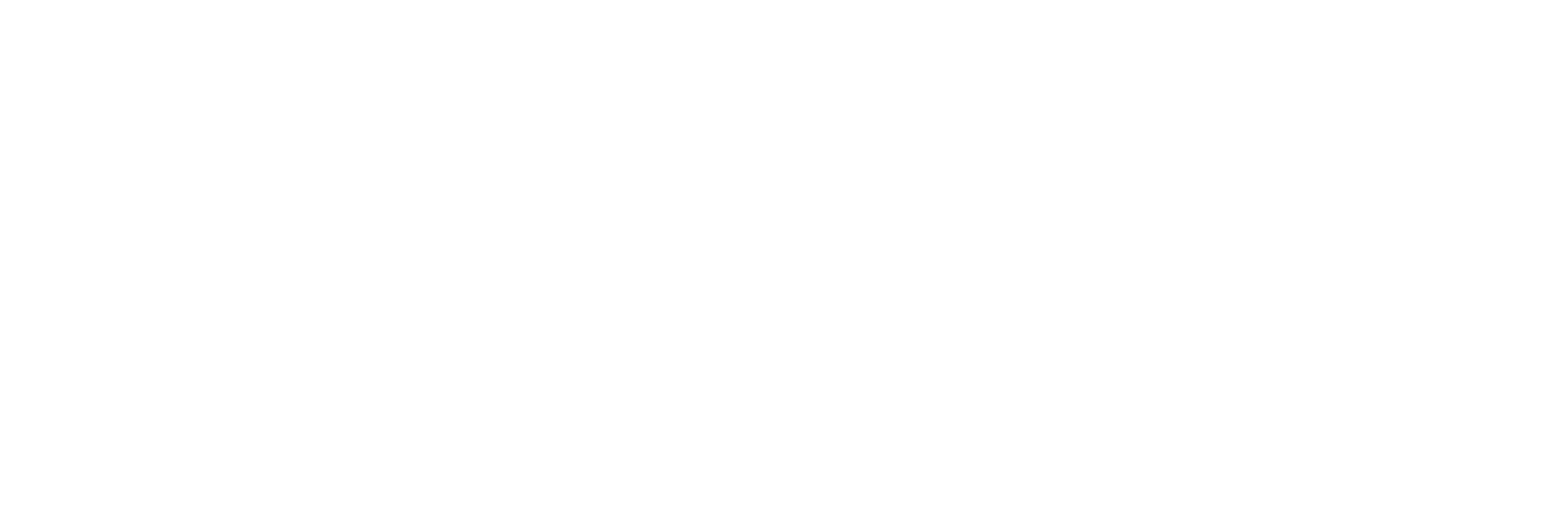
Effective auditing
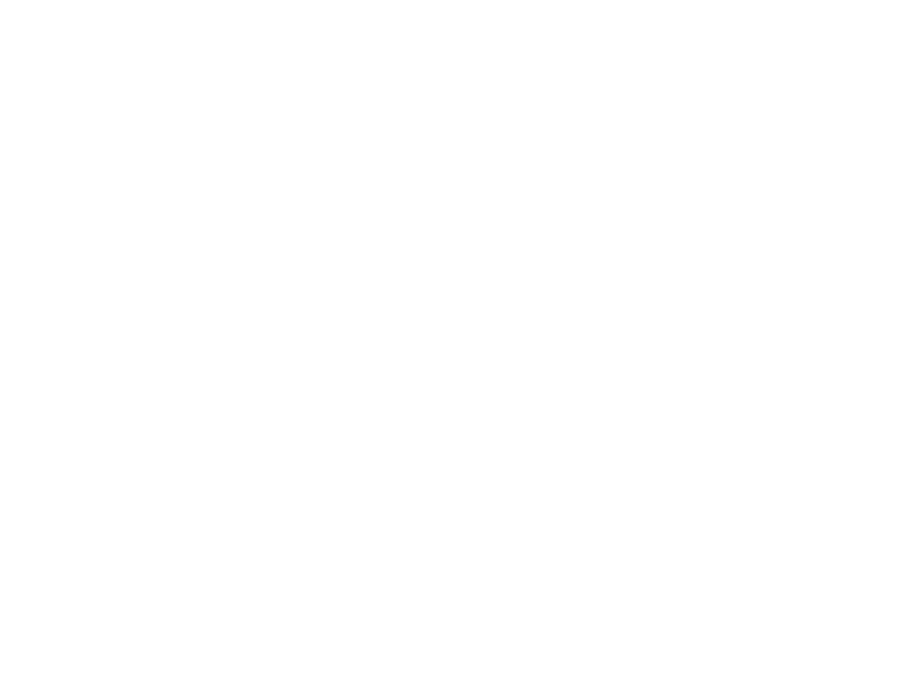
Auditing tools make it possible to ensure that Inditex’s purchasing teams have the precise information they need on supplier compliance with requirements in social, environmental, and product health and safety issues.
Audits are effective when they fulfill this goal, and to this end it is essential that all purchasing teams in the Group’s various retail brands and other business areas are involved in the process. The alignment of sustainability and business strategies is based on responsible purchasing practices.
Inditex has various channels at its disposal to ensure this alignment of purchasing practices and sustainability criteria, guaranteeing the traceability of production and the inclusion of supply chain management as a fundamental pillar of the Group’s business.
CSR teams inform purchasers of audit results in real time using internal tools that involve purchasers in the process of improving the-supply chain. Among the tools used to communicate results, alerts are generated whenever there are changes in compliance with social criteria by a supplier or factory. It is also worth highlighting the control measures applied to all potential suppliers and factories before any orders are formalized by means of a pre-assessment process.
Employee training and awareness raising
Employee training and awareness raising play a very important role in aligning sustainability policies in all of the Group’s business areas. Employees in all areas of the company are trained on aspects of sustainability and maintain fluid contact with CSR teams. In 2014, some 187 new employees at Inditex’s head offices were trained by CSR teams, along with 132 attendees working in purchasing teams within offices in the different clusters.
Training of suppliers
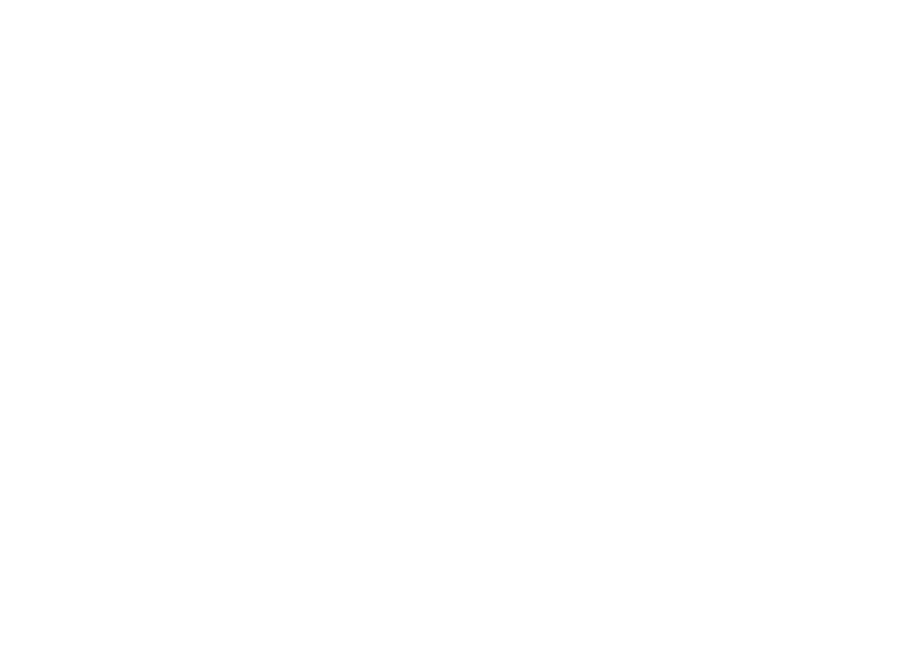
Aware that guaranteeing a sustainable supply chain involves much more than merely monitoring that chain, capacity building of suppliers continues to be a crucial pillar of Inditex’s supply chain management strategy. Inditex is committed to implementing all necessary measures to ensure that factories and suppliers know and understand the contents of the Group’s Code of Conduct, which is intrinsically linked to compliance.
The objective for 2018 is for all suppliers to be included in regular training and capacity-building programmes, and to this end in 2014 the scope of the strategy was expanded to include new countries and projects, adapting training activities to meet the needs of suppliers and imparting 48 training courses and 714 individual sessions to raise awareness among the-supply chain. In this respect, and based on the work carried out in each of the clusters, Inditex’s focus will be increasingly on support for suppliers and the promotion of continual self-assessment. In this way, suppliers will have ever-improving tools at their disposal to optimize their own business and take responsibility for their own supply chain.
Main topics in training plans
- Fundamental labour rights
- Inditex’s Code of Conduct and its compliance
- Production traceability
- Raising awareness of gender equality
- Safety in facilities
Suppliers trained in 2014 by region
Geographic area | Suppliers trained |
---|---|
Africa | 24 |
America | 48 |
Asia | 1,015 |
Europe (non-EU) | 77 |
European Union | 27 |
Total | 1,191 |
Training for women in India
Women make up the majority of workers in the textiles industry in many countries forming part of Inditex’s supply chain. In India, the Shaki project aims to raise awareness and establish gender equality practices in factories based on training for employees, supervisors and management alike in order to avoid and prevent any type of breach of worker rights based on their gender.
With the collaboration of an Indian NGO specializing in health matters, Swasti, 68 suppliers and 11 factories in the country have received training in 2014 on gender awareness and the importance of having mechanisms to prevent discrimination and sexual harassment, including the creation of gender committees in factories. The training involved 195 participants, including factory workers, supervisors and management teams.
Consolidation of the-supply chain
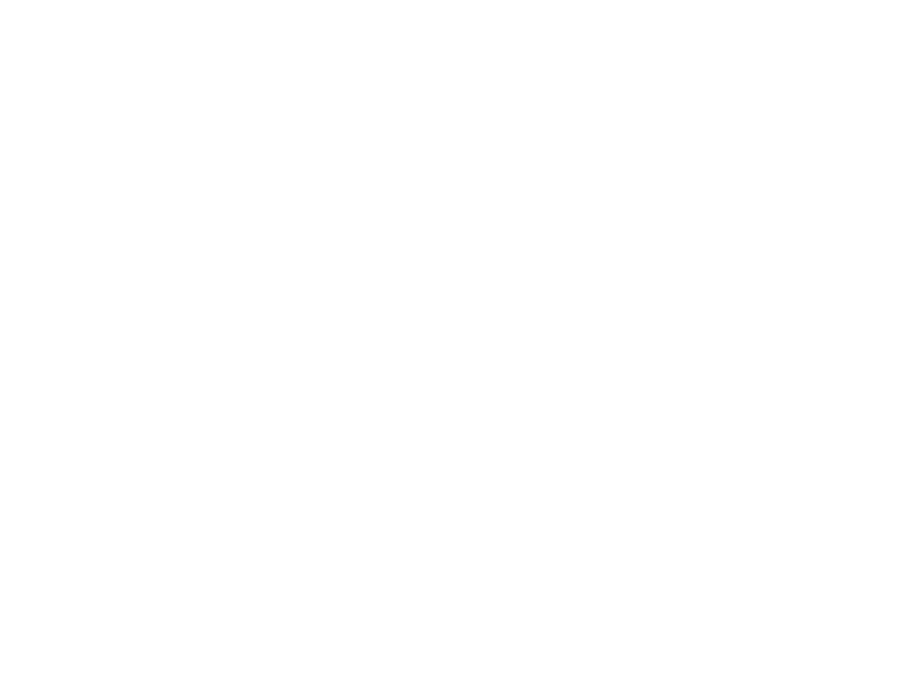
Establishing lasting relationships of trust with suppliers is key to consolidating the-supply chain. This is demonstrated by the improved classification awarded to suppliers according to the way relationships with Inditex are maintained over time.
Suppliers are subject to policies and programmes aimed at protecting the rights of workers from the moment they enter Inditex’s supply chain. The work carried out in clusters allows suppliers to form part of supply chain management by taking responsibility for the factories they work with, and undertaking to fulfil the commitments set out in the Guiding Principles on Business and Human Rights.