3. Strategic Plan 2014-2018. 2016 Review
The Strategic Plan for a Stable and Sustainable Supply Chain 2014-2018 includes identifying and properly knowing suppliers and manufacturers, performing exhaustive assessments and helping them to improve and optimize the social and working conditions of their employees, thus ensuring their sustainability and adjustment to the standards required by Inditex, creating stable and long-term business relations. In 2016 we have reached the halfway of this roadmap, approaching its full implementation with worker-centred programmes.
Strategic Plan for a Stable and Sustainable Supply Chain 2014-2018
I. Identification of the Supply Chain
In 2016, the Inditex supply chain was made up of 1,805 suppliers in 53 countries, working in 6,959 factories:
The Inditex supply chain in 2016*
Geographic area | Suppliers with purchase in 2015 | Suppliers not used in 2016 | New suppliers in 2016 | Suppliers with purchase in 2016 |
Africa | 130 | 13 | 24 | 141 |
America | 74 | 19 | 10 | 65 |
Asia | 836 | 159 | 261 | 938 |
Europe (non-EU) | 185 | 49 | 43 | 179 |
European Union | 500 | 83 | 65 | 482 |
TOTAL | 1,725 | 323 | 403 | 1,805 |
(*) Suppliers of fashion items, mainly clothing, footwear and accessories, with a production of over 20,000 units/year. Suppliers with smaller production account for 0.29% of total production.
To correctly identify the supply chain we use complementary monitoring, verification and adaptation tools.
To this end, our sustainability team employs engineers specializing in production systems and processes, production planning methods, and so on. This way, the traceability management is enriched with a technical vision which, added to the social vision, increases the effectiveness of the traceability audits.
In 2016, a total of 2,776 traceability audits were carried out. In these audits, both the internal and external Inditex teams worked in situ to verify that production of the Group’s brands was taking place in correctly declared and authorized factories. In 2016, the percentage of compliance was 89%. The 309 non-compliances that the internal and external teams detected relate, above all, to a lack of information. And they have been dealt with specifically by the sustainability and procurement teams.
Traceability audits in 2016
Geographic area | 2016 |
Africa | 388 |
America | 1,313 |
Asia | 617 |
Europe (non-EU) | 418 |
European Union | 40 |
Total | 2,776 |
Year after year, our suppliers are more aware of the importance of transparency and traceability throughout the entire production process, and are committed throughout the factory declaration procedure. In cases of non-compliance or a lack of transparency, the sustainability and purchasing teams worked together with the supplier to obtain a commitment from them on implementing the measures required. Each case is analysed by sustainability teams, which apply a common maxim throughout the Strategic Plan: opportunity for improvement but zero tolerance for repeated non-compliance. Relations were severed with 17 suppliers on these grounds in 2016.
II. Assessment of the supply chain
Compliance programme
AUDITS IN 2016
TOTAL AUDITS: 10,883At Inditex, suppliers and manufacturers are first evaluated before they enter our supply chain through a Pre-Assessment audit. In 2016, some 2,302 pre-assessment audits were performed, of which 81% had a positive outcome. The number of such audits has declined compared to 2015, when we conducted 2,703. This fact that reveals the progressive consolidation of the supply chain, since each new factory registered by a supplier is audited.
PRE-ASSESSMENT AUDITS IN 2016
Geographic area | Pre-assessment audits | % Approved |
Africa | 71 | 85% |
America | 19 | 63% |
Asia | 1510 | 75% |
Europe (non-EU) | 350 | 89% |
European Union | 352 | 98% |
Total | 2,302 | 81% |
In 2016, the Pre-Assessment Audit methodology was updated. The changes in methodology were based on the experience gained since the previous review, conducted in 2012. In order to carry it out, the best practices, experiences and proposals for improvement of all local sustainability teams have been collected and 39 representatives of external auditing companies were trained with the train the trainer methodology so that, in turn, they can train their respective teams. The result reinforces this first assessment, which increases the level of demand and maintains the maxim of ensuring that only suppliers and manufacturers that comply with our Code of Conduct enter the supply chain.
After the Pre-Assessment audit, all companies producing for Inditex face periodically social audits. With this we re-evaluate their degree of compliance with the Code of Conduct and assign them a rating based on it. In 2016, 4,011 social audits were carried out, 187 more than in 2015.
Social audits are conducted by external and internal auditors. The procedure is the same regardless of who performs them, since in Inditex we have our own social audit methodology. This methodology was developed jointly by Inditex, IndustriALL Global Union, the Cambridge Centre for Business and Public Sector Ethics and the University of Northumbria (UK). Its application allows a complete and detailed evaluation of the factories and suppliers and identifies their strengths and their improvement needs.
The time that elapses until the next social audit varies according to the ranking obtained. However, all factories and suppliers are socially audited on a regular basis, regardless of the performance of other audits or programmes to which they are subject. Moreover, after the social audit, the results are analysed to identify areas for improvement at both individual and aggregate levels in a geographic area in order to establish the necessary programmes.
SOCIAL AUDITS IN 2016
Geographic area | Total |
Africa | 191 |
America | 288 |
Asia | 2,022 |
Europe (non-EU) | 685 |
European Union | 825 |
Total | 4,011 |
Social audits assess suppliers’ compliance with each and every section of the Code of Conduct. In 2016, the requirement level of health and safety at work increased, which has led to an increase in health and safety-related programmes in a greater number of countries and factories. Our auditors are specialized in this aspect, which allows them to detect various breaches and go further in their evaluations.
In 2016, 95% of the production was carried out by suppliers with A or B qualification, the two highest compliance levels within Inditex's own rating methodology. Likewise, the percentage of suppliers with a C ranking, which fails to comply with one or more sensitive aspects of the Code of Conduct, fell by two percentage points compared to 2015, as a result of the continuous work with suppliers to improve working conditions.
What is a social audit?
Classification of suppliers with purchase in 2016(*)
2016 | 2015 | |||||
Classification* | Suppliers | % Suppliers | % Production | Suppliers | % Suppliers | % Production |
A | 694 | 38% | 40% | 724 | 42% | 41% |
B | 917 | 51% | 55% | 794 | 46% | 54% |
C | 83 | 5% | 1% | 116 | 7% | 3% |
CAP | 61 | 3% | 3% | 35 | 2% | 1% |
RP | 50 | 3% | 1% | 56 | 3% | 1% |
Total | 1,805 | 100% | 100% | 1,725 | 100% | 100% |
(*) Supplier A: complies with the Code of Conduct
Supplier B: breaches a non-material aspect of the Code of Conduct
Supplier C: breaches a sensitive aspect of the Code of Conduct
Supplier subject to Corrective Action Plan (CAP): breaches of the Code of Conduct, requiring the immediate implementation of a Corrective Action Plan
PR supplier: undergoing an auditing process.
Percentage compliance with the Code of Conduct in active factories (*) associated with suppliers with purchase in 2016
(*) Does not include factories rejected in 2016.
(**) Includes the lack of suitable systems for checking the age of workers.
(***) Includes the lack of suitable systems for registering and informing workers.
Special audits are other type of evaluations carried out and are focused towards a specific area of improvement. Examples of objectives addressed in these visits are structural technical assessments, the review of laundry processes to verify that practices prohibited by Inditex such as sandblasting are not carried out, or the assessment of workers' working conditions from an exclusively health and safety point of view. Also included in this category are competence visits to verify the progress of Corrective Action Plans.
Year by year the number of special audits increases progressively; this is also seen in a greater specialization of our sustainability teams, among which there is an increasing number of specialized technicians in each area. Thus, in 2016, 1,794 special audits were carried out, compared to 1,584 in 2015. Of these, 183 were specific audits to verify the conditions of workers from the health and safety perspective.
SPECIAL AUDITS IN 2016
Geographic area | Special |
Africa | 127 |
America | 26 |
Asia | 1,418 |
Europe (non-EU) | 141 |
European Union | 82 |
Total | 1,794 |
III. Optimization of the supply chain
The evaluation of the supply chain must be accompanied by optimization actions to advance its sustainability and the improvement of working conditions. At Inditex we believe in continuous improvement as a key element in our daily relations with suppliers, so throughout the business relationship we help and collaborate to optimize their management systems to the workers’ benefit.
The detection of any type of non-compliance implies the immediate implementation of a Corrective Action Plan. This plan establishes all improvement actions that the factory or supplier must perform to correct the non-compliances detected in the audit, as well as the deadline for this, which will be more or less restrictive depending on the seriousness of the breach detected. In this regard, we firmly believe that helping factories to improve their conditions brings the best possible results for workers, as well as contributing positively to the consolidation of a stable and sustainable supply chain. And we leave rejecting a factory as the last option.
We constantly support our suppliers and manufacturers in the development of the Action Plans. The participation and support of the purchasing teams is very important in this process. As well as Inditex's internal teams, members of civil society such as unions or NGOs participate in Corrective Action Plans. As an example, in 2016, the participation of IndustriALL Global Union and its local affiliates, the Refugee Support Centre in Turkey or the NGO Pratham in India stand out.
A key milestone in the improvement of a factory is the competence visit, in which Inditex’s internal team analyses
Corrective Action Plans (CAP) focus on factories or suppliers where non-compliance with sensitive points in the Code of Conduct has been identified. In these cases, monitoring and follow-up is much stricter, limiting its duration to six months. After this period, a new social audit is carried out to ensure that the necessary corrections have been carried out. If the social audit proves that the Corrective Action Plan has not been fulfilled, the factory or supplier will be blocked.
In 2016, 453 factories with breaches at sensitive points in the Code of Conduct initiated a Corrective Action Plan. It should be noted that the number of factories involved in this type of Corrective Action Plan has been decreasing over the last four years, despite the increase in audits. This demonstrates how collaboration and daily work in close contact with suppliers and manufacturers result in a better level of compliance. And how suppliers are increasingly proactive in adapting their conditions to the Code of Conduct.
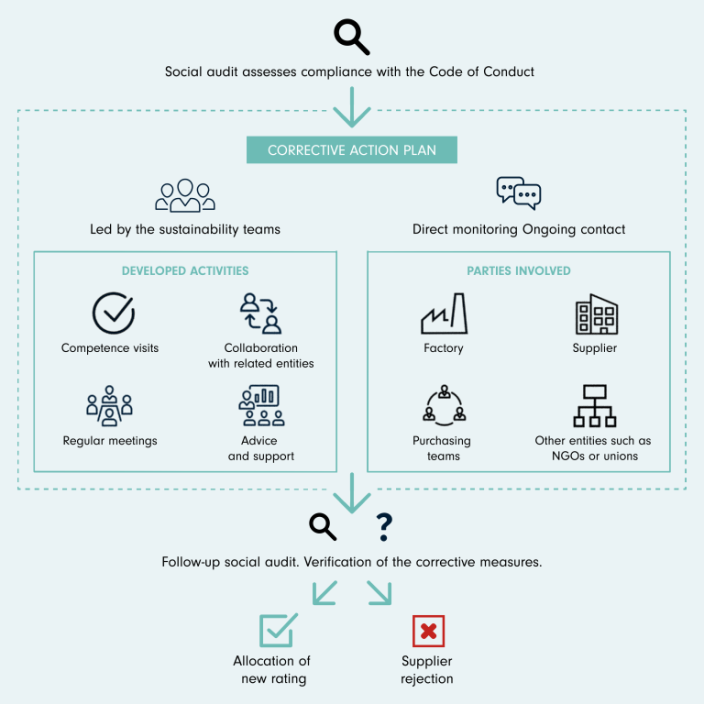
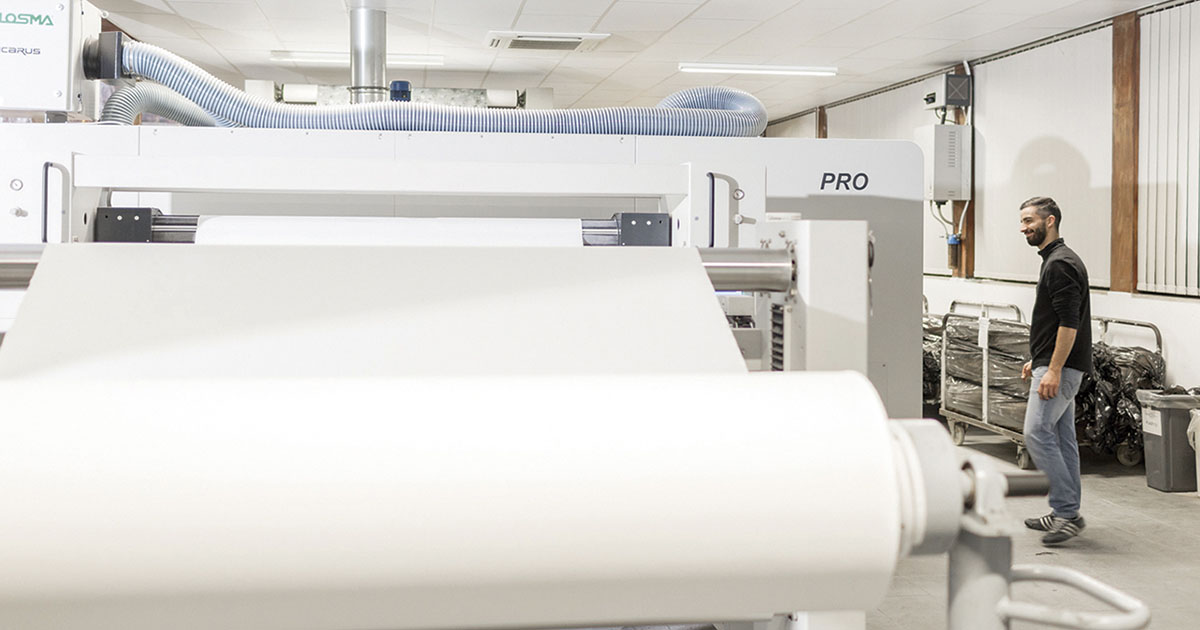
TRENDS IN THE EVOLUTION OF SOCIAL AUDITS AND CORRECTIVE PLANS (*)
Inditex bases its relationships with suppliers on mutual trust and on a philosophy of continuous optimization whereby opportunities for improvement are encouraged. However, we also maintain a zero tolerance attitude towards those who do not take advantage of these opportunities and do not comply with the Code of Conduct or with the requirements for working with us. Thus, of the 1,805 suppliers used in 2016, 76 were rejected during the year for failing to comply with the conditions necessary to work with Inditex. This includes both business and sustainability-related reasons. In this regard, 41 suppliers were blocked due to some type of non-compliance with the Code of Conduct.
Suppliers rejected in 2016
Geographic area | Suppliers with purchase* | Rejected due to breach of the Code of Conduct | Rejected for commercial reasons | Active suppliers at 31/01/2017 |
Africa | 141 | 2 | 0 | 139 |
America | 65 | 3 | 6 | 56 |
Asia | 938 | 15 | 25 | 898 |
Europe (non-EU) | 179 | 15 | 2 | 162 |
European Union | 482 | 6 | 2 | 474 |
Total | 1,805 | 41 | 35 | 1,729 |
(*) Suppliers with purchase in 2016 of fashion items, mainly clothing, footwear and accessories, with Inditex production of over 20,000 units/year.
Inditex continuously works hand-in-hand with its suppliers, in line with the objective of establishing stable and lasting relationships. Therefore, we seek to cooperate closely with our suppliers with a constant dialogue where trust is mutual. The benefits of daily work from the outset with the supplier can be seen in how suppliers’ classifications improve with the years of relationship with Inditex. Thus, the percentage of suppliers with ranking A and B is higher among those suppliers that have been collaborating with Inditex for over three years and taken part in several programmes under the 2014-2018 Strategic Plan.
Supplier RATING according to years of commercial RELATION with Inditex (%)
Supplier B: breaches a non-material aspect of the Code of Conduct
Supplier C: breaches a sensitive aspect of the Code of Conduct
Supplier subject to Corrective Action Plan (CAP): breaches of the Code of Conduct, requiring the immediate implementation of a Corrective Action Plan
PR supplier: undergoing an auditing process.
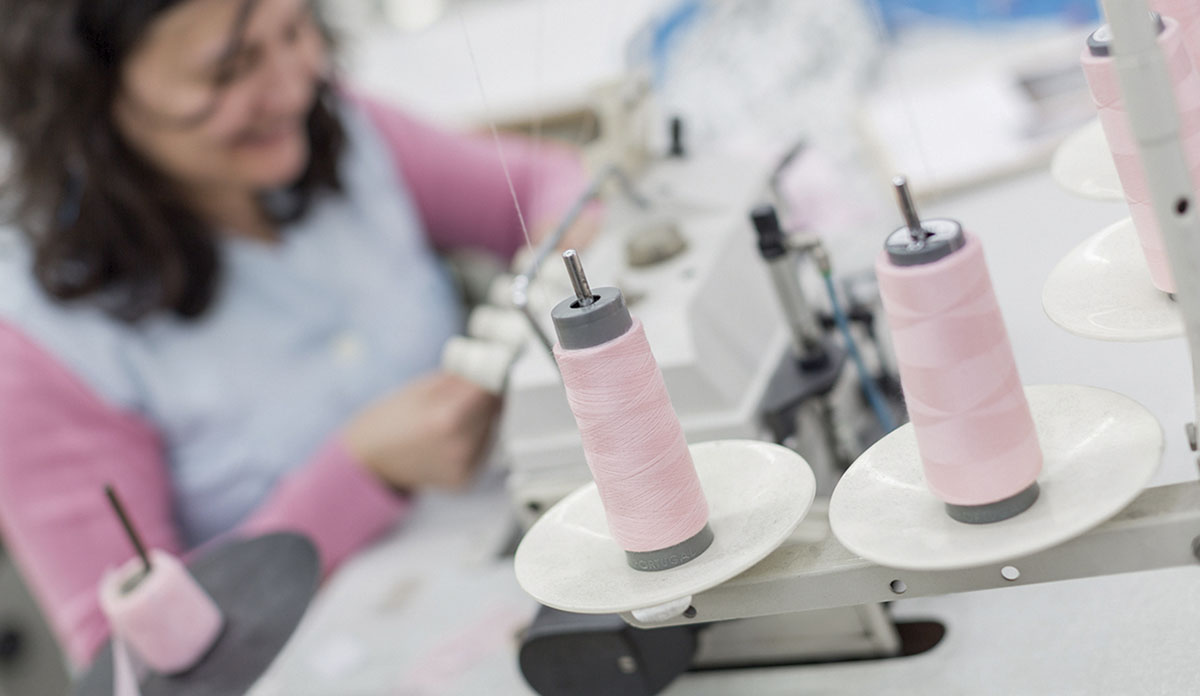
IV. Sustainability
To ensure that the activities of our suppliers have a positive impact on the communities where they operate, Inditex cooperates with global and local stakeholders. In addition to our Global Framework Agreement with IndustriALL, we join forces with various local, regional and international initiatives and organizations to promote sustainability in the textile sector and, consequently, improve the quality of life of communities dependent on this industry. This is done through clusters that Inditex defines as cooperation spaces for promoting a sustainable production environment in a strategic geographical area and within a framework of compliance with Human Rights and Fundamental Labour Rights.
Currently, we have clusters in Spain, Portugal, Morocco, Turkey, India, Pakistan, Bangladesh, Vietnam, Cambodia, China, Brazil and Argentina that account for more than 95% of our production and contribute to our social and labour standards being applied locally. Pakistan is the last to be created, with the aim of responding to local challenges and in close proximity to suppliers and their workers.
Internal and External TEAMS IN CLUSTERS
Cluster | Internal team | External team |
Spain | 14 | 14 |
Portugal | 2 | 28 |
Morocco | 4 | 12 |
Turkey | 9 | 26 |
India | 6 | 71 |
Bangladesh | 10 | 28 |
Vietnam | 2 | 20 |
Cambodia | 1 | 19 |
China | 11 | 321 |
Brazil | 1 | 26 |
Argentina | 2 | 7 |
Pakistan | 1 | 15 |
Total | 63 | 587 |
Main cluster collaborations
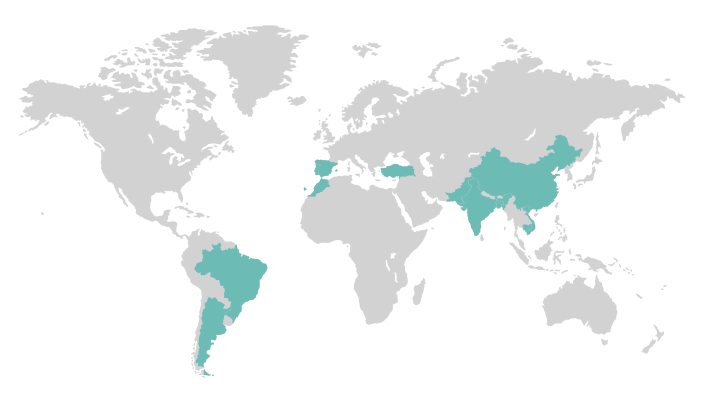
Activities in clusters in 2016
Spain | Portugal | Morocco | Turkey | India | Bangladesh | |
IDENTIFICATION | ||||||
Traceability audits | Coordination traceability strategy | 40 | 388 | 418 | 12 | 52 |
Suppliers with purchase during the year | 208 | 170 | 121 | 175 | 136 | 94 |
Active factories in the year | 466 | 1,357 | 283 | 1,427 | 394 | 262 |
Workers in active factories | 10,298 | 49,714 | 73,772 | 192,173 | 200,139 | 479,859 |
ASSESSMENT | ||||||
Audits | ||||||
Pre-Assessment | 71 | 158 | 48 | 327 | 214 | 78 |
Social | 50 | 694 | 155 | 679 | 392 | 190 |
Special | 82 | 127 | 141 | 379 | 739 | |
Rating of suppliers | ||||||
A suppliers | 99 | 88 | 51 | 82 | 71 | 38 |
B suppliers | 70 | 69 | 54 | 68 | 55 | 51 |
C suppliers | 9 | 4 | 6 | 5 | 6 | 2 |
CAP suppliers | 2 | 8 | 8 | 15 | 4 | 3 |
OPTIMIZATION | ||||||
Corrective Action Plans | 1 | 86 | 40 | 160 | 61 | 15 |
SUSTAINABILITY | ||||||
Featured initiatives | Coordination of global strategy and representation in the UN Global Compact or Ethical Trading Initiative, among others. | Training and work experience for young students of the Catholic University of Porto. | Health and safety programme in factories and collaboration with Medicus Mundi Andalusia for the health and hygiene of workers. | Joint Turkey Programme to improve productivity and social dialogue, training project with IndustriALL. | Sakhi Health and Sakhi Gender Equity Programmes for women empowerment, Sowbhagyam Programme for eradicating sumangali, Sankalp Programme for eradicating child labour. | Participation in Accord, effective implementation of participation committees with IndustriALL, reinforcement of internal health and safety programmes |
Vietnam | Cambodia | China | Brazil | Argentina | Pakistan | |
IDENTIFICATION | ||||||
Traceability audits | 53 | 156 | 344 | 318 | 995 | 0 |
Suppliers with purchase during the year | 4 | 1 | 393 | 15 | 45 | 42 |
Active factories in the year | 134 | 125 | 1,654 | 65 | 83 | 107 |
Workers in active factories | 152,101 | 126,843 | 368,428 | 10,712 | 5,099 | 125,316 |
ASSESSMENT | ||||||
Audits | ||||||
Pre-Assessment | 50 | 59 | 1,019 | 9 | 9 | 30 |
Social | 101 | 74 | 1,133 | 161 | 104 | 90 |
Special | 18 | 138 | 144 | 18 | 8 | 0 |
Rating of suppliers | ||||||
A suppliers | 2 | 0 | 45 | 14 | 37 | 23 |
B suppliers | 1 | 1 | 301 | 0 | 3 | 18 |
C suppliers | 1 | 0 | 35 | 0 | 0 | 0 |
CAP suppliers | 0 | 0 | 8 | 0 | 3 | 1 |
OPTIMIZATION | ||||||
Corrective Action Plans | 9 | 1 | 72 | 0 | 5 | 2 |
SUSTAINABILITY | ||||||
Featured initiatives | Participation in Better Work Vietnam with 13 factories | Participation in Better Work Cambodia with 54 factories | SCORE Programme with ILO, LEAN Project, health and safety training in collaboration with EHSA Centre, Ling’nan University | Participation in an Agreement with ILO to promote improvements in the working conditions of workshops in Sao Paulo | Collaboration with the National Institute of Industrial Technology to develop production monitoring criteria. | Participation in the Buyers Forum of Pakistan |