3. SUSTAINABLE MANAGEMENT
In 2012, Inditex adhered to the Zero Discharge of Hazardous Chemicals Commitment to minimize the environmental impact of our production and to improve the health of our garments and the safety of our employees in the supply chain. Since then, we have oriented our strategies to control and improve of manufacturing towards eliminating hazardous chemical substances before 1 January 2020. In 2016, this commitment materialised in three programmes where the objectives were to work on: the identification of hazards in the entire manufacturing chain; the substitution of the substances included in the Manufacturing Restricted Substances List (MRSL); and the transparency of these processes.
Identification of Hazards: Inditex designs and implements a programme that allows the identification and elimination of hazardous substances in the supply chain. We are completing the first exhaustive compilation of all chemical substances used in the textile and leather industry.
Also, we are working on an R&D programme to classify the chemical substances used in our manufacturing processes. With this information, we have created our own MRSL, which includes products which are prohibited for use in the manufacturing processes of our garments.
Responsible substitution: Inditex undertakes the substitution of the substances included on the MRSL in a responsible manner, always using the safest alternatives.
- Complete elimination of the use of PFCs en nuestros artículos, estudiando y promoviendo la adopción de alternativas seguras a estas sustancias.
- Implementation of the clean factory strategy for the elimination of the use of APEOS, chemical substances mainly used in the removal of oil stains.
Transparency: Inditex informs the public of its findings in this area with complete transparency. Thus, the MRSL, the full list of the facilities with wet processes involved in our supply chain, the discharges analysed and the complete reports of the actions developed can be found at www.wateractionplan.com
RESPONSIBLE MANUFACTURING
In 2016, Inditex sold over 1.3 billion items, including garments, footwear and accessories. In order to ensure that these items reach our customers in compliance with the strictest standards, it is necessary to carry out an evaluation of all operations, processes and protocols to which the garments are subject.
At Inditex, we make great efforts to ensure that the production process of our items, from the selection of the components to the finished product, can be as flexible and efficient as possible, in keeping with our business and distribution model. Also, completing the process in a safe and sustainable manner requires exhaustive knowledge of the supply chain and complete preparation and supervision of the facilities and the products used.
OUR PROGRAMMES IN THE MANUFACTURING OF A GARMENT | ||||||
Facilities used in the manufacturing of a garment | SPINNING | WEAVING | DYEING | PRINTING | WASHING/FINISHES | TAILORING |
Types of chemical products used in the different facilities | Lubricants | Gluing products | Desizing agents, detergents, bases, acids, bleaches, colours and fixatives | Pigments, colorants, coatings, fixatives, adhesives and detergents | Coatings, fixatives, adhesives and detergents | Adhesives |
Application of our programmes | The List | The List |
The List Ready to Manufacture |
The List Ready to Manufacture |
The List Ready to Manufacture |
The List Picking |
This supervision process begins long before the first textile is dyed or the manufacturing has begun. Establishing that the chemical products and the manufacturing facilities that will be used are the most suitable is the first step. Thus, for Inditex it is essential to collaborate with scientific and technological partners for the design and elaboration of the work tools, with expert auditors for the supervision of the facilities, materials and processes used, and finally, with our suppliers.
The selection and adequate use of chemical products for the manufacturing and finishing of the textiles, the use of appropriate manufacturing techniques and the traceability of the raw materials and production processes, are key for responsible manufacturing. Inditex ensures that the facilities designated for manufacturing each item correctly execute each of these actions through two programmes in the supply chain, The List by Inditex and Ready To Manufacture (RTM).
The final processing of each item must comply in order to be commercialised with our strict health and safety standards, Clear to Wear (CtW) and Safe to Wear (StW).
Furthermore, before each production is completed and received, Inditex submits a representative sample of these finished items for chemical evaluation and analysis. For this, we use a system that flexibly and efficiently adapts to the logistical and production terms that are characteristic of the business model. This control system is the Picking Programme.
If the production does not comply with health and safety requirements, the garments are not accepted and a protocol is launched in order to determine the cause(s) of the non-conformity, avoiding repetition in future productions: Root Cause Analysis (RCA).
MAXIMUM TRANSPARENCY OF OUR PROGRAMMES: PROGRESS IN 2016
Clear to Wear product health standard
Before initiating manufacture, it is of vital importance to know the requirements that the items must comply with, i.e., it is necessary to identify the limited chemical substances and their permitted levels in the end product. These requirements are the base of our product health standard Clear to Wear (CtW) where the publication document, unlike the common Restricted Substances Lists (RSL), is a reference manual with information on regulations, analysis methods and legal limits, among other information.
To develop this, we have a team of scientists and technology experts that place CtW at the cutting edge of product chemical restrictions, as it also includes substances that are not legally limited. During 2016, Inditex introduced new features and updates in the CtW standard, which will be applicable in 2017.
Inditex’s position is clear: maximum responsibility and demand, in line with a total commitment to customers and to the 93 markets with different regulations where we are present. In this regard, Clear to Wear, the first version of which was published over a decade ago, constitutes the most complete and demanding regulatory framework that, as well as being on the cutting edge for substances to restrict, includes all of the most demanding international regulations as a minimum requirement.
NEW SUBSTANCES REGULATED IN THE CLEAR TO WEAR STANDARD SINCE 2017
THE LIST BY INDITEX
The List by Inditex is a unique and pioneering global programme that, through industry collaboration, aims to improve the quality of chemical products used in the manufacture of textile and leather items. Its objective is to ensure, in an efficient and definitive manner, compliance with the Clear to Wear standard and, secondly, the Commitment to Zero Discharge of Hazardous Chemicals 2020.
The methodology for participating companies for the supervision and control of the chemical products that appear on The List includes, among other protocols, the performance of chemical analyses, audit of factories where these substances are produced and, above all, strict supervision of companies’ product safety policies.
In collaboration with the chemical industry, The List presents two different time scales:
- In the short term, it works on the identification and restriction for use of hazardous chemical products, both from the perspective of Health and Safety, and its impact on the environment.
- In the long term, it works on improving the entirety of chemical products through perfecting the existing production procedures. In cases where this perfecting is not possible, it works with R&D programmes that permit the creation of new chemical products that are alternatives to those existing.
Ready to Manufacture
Ready to Manufacture (RTM) is Inditex’s manufacturing code, pioneering and unique in the textile industry, which through actions at the wet process facilities (dyeing, washing, printing and tanneries) seeks compliance with the Inditex product safety standard Clear To Wear and our commitment to achieve Zero Discharge of Hazardous Chemicals in 2020.
Correct implementation of RTM in the supply chain guarantees compliance with our CtW product safety standard and the Commitment to Zero Discharge at the facilities through the application of:
- Responsible manufacturing processes that include, among other actions, the correct selection of chemical products and manufacturing conditions.
- A strict programme for supervision and control of production that establishes rigorous analysis in products and processes identified as hazards.
The implementation of responsible manufacturing practices included in RtM minimises non-compliance with our standards detected in the control programmes. In this way, we reduce the need to reprocess operations in order to achieve the desired finishes and improve the efficiency of our sustainable manufacturing processes, by minimising additional consumption of resources (chemical products, water and energy) required for these second operations.
NON-COMPLIANCE RATE FOR CLEAR TO WEAR AND IMPROVEMENTS UPON APPLICATION OF READY TO MANUFACTURE
This graph shows the reduction of reprocessing reached in a facility by applying the RtW standard. On the one hand, there is a reduction in all internal non-compliance associated with restricted chemical substances (arylamines and formaldehyde) and, on the other, there is a significant reduction in reprocessing due to non-compliance with parameters such as pH (reduction of 80%) or fastness (reduction of 60%).
ENVIRONMENTAL SUSTAINABILITY IN THE GREEN TO WEAR STANDARD
One of our strategic objectives for 2020 is to reach Zero Discharge of Hazardous Chemicals in our entire supply chain. To achieve this, we have developed the project on Capacity Building in the Supply Chain. At the same time, we continue to implement our own Green to Wear standard, which includes our efforts in the wet processes of the manufacturing: dyeing, printing, washing, tanning and finishing. Based on the Clean Factory approach, we promote the best techniques available for efficient environmental management and sustainable chemistry.
Through these tools, we evaluate the status of our value chain and provide training resources and instruments for analysis to our suppliers. Thanks to the Capacity Building project for suppliers, we are progressing towards the sustainability of the wet process plants so that they can continuously improve their efficiency and performance.
Specifically, we work in areas associated with the handling of the raw materials, water, energy, chemical products, wastewater and waste. In just three years, we have carried out 729 environmental evaluations in wet process factories. This has allowed us to progress towards compliance with our commitment to Zero Discharge, improving traceability and achieving a more transparent and less intensive production process for the consumption of resources.
With each evaluation, we carry out an Environmental Monitoring Plan, which allows our suppliers to identify and optimise the areas of the facility where improvements can be made for the environment. We also verify compliance with the discharge parameters at the purification facilities, the size and optimal management that allow correct purification of the water derived from the manufacturing processes.
Since 2014, we also verify compliance with our PFC Free policy so that all of our products are free from perfluorocarbons (PFCs), compounds used in the waterproof and water repelling finishes. Given that this is of obligatory compliance in our supply chain, in 2016 we have worked with 160 direct suppliers in order to provide alternative sustainable solutions for these unwanted substances.
We are also committed to the transparency of our progress towards Zero Discharge. In 2016, we published the list of our suppliers related to the wet processes.
To support the achievement of these objectives, we collaborated with various universities and technological centres to detect alternatives based on sustainable chemistry, the promotion of clean technologies and the creation of training material. Among the available materials are technical sheets developed in collaboration with the University of A Coruña.
These documents analyse, for each of the different stages in the purification process, the different systems and technologies existing. These are key in helping our suppliers to improve the purification of wastewater and to reduce the discharge of chemical substances. They are available on our website: www.wateractionplan.com
Picking Programme
The Picking Programme is our instrument for verifying the quality of the items commercialised by Inditex. It is structured in various stages, among which we can highlight the decision of the analyses, the taking of representative samples from productions and the performance of analysis in external analytical laboratories.
The laboratories, distributed throughout the principal manufacturing geographical clusters, are the key actors for Picking and, for this reason, work in a standardised manner. Optimised analytical methods are used, with strict monitoring of quality.
The keys of the Picking Programme

Efficacy and efficiency in the analysis decision
The first step in the control of production is to decide upon the substances/parameters, the items and parts to be controlled. Together with the University of Santiago de Compostela, Inditex has developed tools to detect non-compliance with the Clear to Wear standard. In 2016, 619,854 analyses and tests were carried out, implying optimisation of 29% with regards to the previous year. The positive evolution of the suppliers in compliance with the Product Health and Safety, together with the actions of control programmes during the production (RtM and The List) have allowed for adaptation of the number of analyses carried out without compromising the compliance guarantee of our products.
Production representativeness
At Inditex, we perform careful sample taking that guarantees that the results of the analyses carried out are representative of the entire production they originate from.
Adaptation to the Inditex manufacturing model
Inditex uses an analysis network of 64 external laboratories distributed throughout the main manufacturing countries, the number of which is reviewed and increased annually.
Optimised analysis methods
The laboratories linked to the Picking Programme use optimised analysis methods that permit, on the one hand, significant reduction of the response times and, on the other, increased analysis capacities.
Excellence in the execution of the analyses
The decision on whether to accept or reject production is taken based on the number of analyses carried out on the same. For this reason, the precision and accuracy of the analyses must be maximum.
Inditex guarantees the quality results of all laboratories in the network through a quality supervision programme for the test procedures and qualifications of the technical personnel, designed and executed in collaboration with the University of Santiago de Compostela.
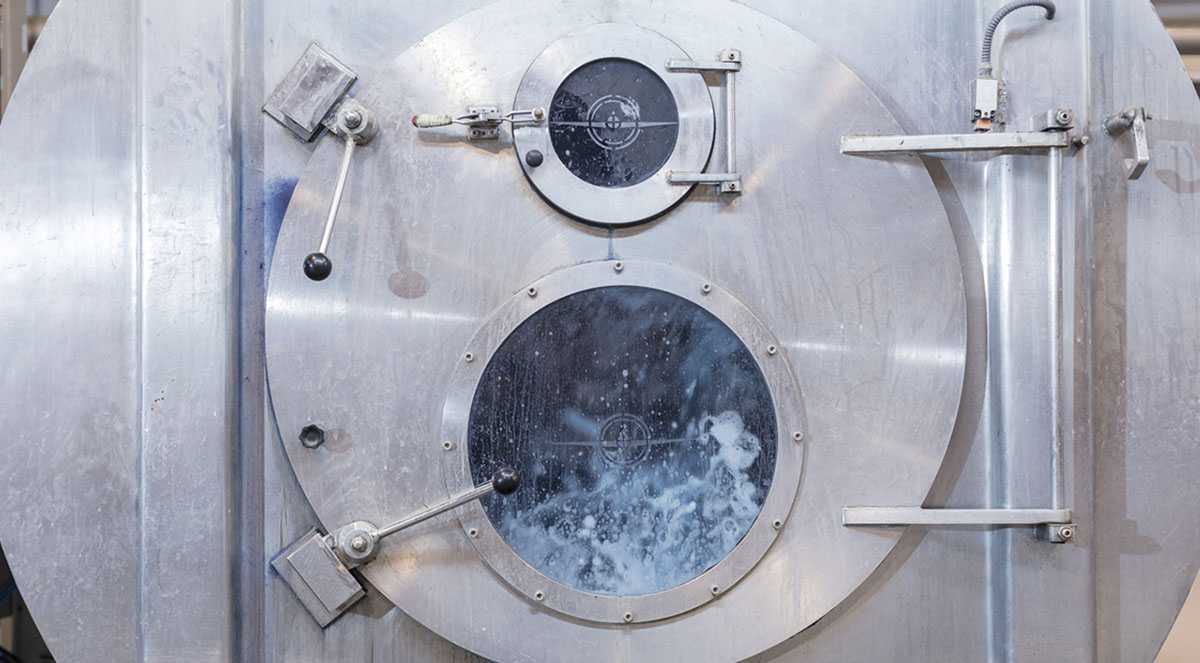
Root Cause Analysis (RCA)
When an item does not comply with Health and Safety requirements, Inditex rejects production and carries out a Root Cause Analysis (RCA). In this type of analysis, experts from the textile and/or leather sector visit the facilities (dye, wash, print and tannery) involved in the manufacturing of the item affected in order to determine the origin of the incident. Finally, a Corrective Action Plan is provided for the facility in order to avoid the repetition of the incident in the future.
It should be noted that both the incidents detected through the RCA and the solutions provided to the facilities are used as feedback in the manufacturing intervention programmes: Ready to Manufacture and The List by Inditex, which ensures constant improvement of the same.
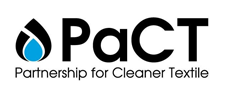
COLLABORATION WITH PROGRAMMES FOR SUSTAINABILITY IN THE TEXTILE SECTOR
At Inditex we support the Partnership for Cleaner Textile in Bangladesh (PaCT). This initiative works in collaboration with the World Bank in order to improve competitiveness of the textile sector through adopting the better practice in the management of water, energy and chemical substances.
For this, we collaborate in the development of specific technical materials and in the improvement of access to funding for investments for more sustainable production.
Thanks to the participation in this initiative, a total of 18.4 million cubic metres of water have been saved, 15.9 million cubic metres of wastewater have been avoided, and 275,346 tonnes of CO2 have not been emitted.
Another initiative that we joined in 2016 is the Clean by Design (CBD) programme, together with the Natural Resources Defence Council (NRDC), to promote sustainability in textile production in China.