2. SUPPLY CHAIN PROGRAMMES: WORKERS AT THE CENTRE
The more than one and a half million workers in the Inditex supply chain are our priority when designing programmes and initiatives that aim to ensure their well-being. At Inditex we want these factories –in over 50 countries and with diverse social and cultural circumstances– to be places of work where the highest labour, health and safety standards are guaranteed. We also want these factories to be spaces where human rights are respected and promoted.
To this end, we design programmes in the different clusters that cover aspects as diverse and important as training, representation, occupational health and safety or wages. These projects and lines of work are in areas we believe need to be strengthened, once the results obtained in the Compliance Programme have been analysed.
In turn, all projects are related to relevant Human Rights and allow us to focus our efforts on the most vulnerable groups in the supply chain.
The different programmes have been created with the aim of covering 100% of the supply chain and covering all the workers that form part of it, although the implementation is progressive and is carried out taking into account each country’s specific needs. To this end, the local circumstances, strengths and areas of improvement are analysed in detail through due diligence processes, in order to develop, as a priority, the most relevant programmes for each community.
Below are the most relevant programmes of 2016, as well as the performance of the initiatives that make up the Strategic Plan for a Stable and Sustainable Supply Chain 2014 - 2108. Each programme’s most representative indicators are included.
Workers at the centre
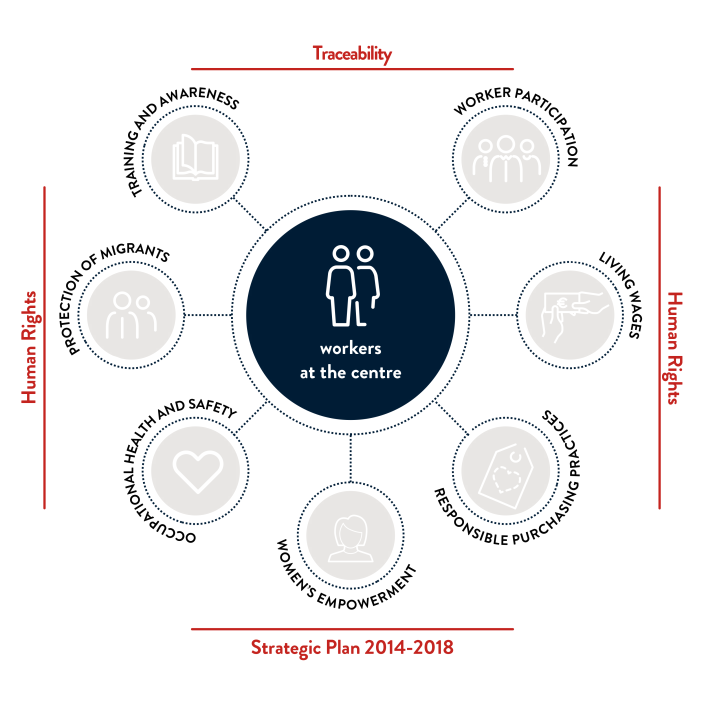
I. Worker participation
One of our most valuable mechanisms for workers' participation is the Global Framework Agreement (GFA), signed in 2007 with the international union federation IndustriALL Global Union, which in October 2017 will have been established for 10 years.
During these years, collaboration and dialogue with IndustriALL has been constant, a fundamental factor to contributing to a better balance of labour relations in the supply chain. This has also favoured the objective established by Inditex in its Strategic Plan 2014-2018 to maintain a stable and sustainable supply chain.
The Framework Agreement, which covers the entire supply chain, is intended to protect the interests of workers in the factories with which Inditex works and ensure compliance with trade union rights and other labour rights. During this time, Inditex and IndustriALL have developed numerous joint initiatives in the clusters. The relationship between Inditex's local teams and IndustriALL's delegations is continuous, which allows us to approach the workers and learn their needs and expectations.
The main collaborative tools and lines of work of the Framework Agreement are:
- Supply chain transparency. Inditex shares all the information related to its supply chain and its degree of compliance with the Code of Conduct with IndustriALL and facilitates the access by the unions to all its suppliers’ facilities, allowing both parties to evaluate the conditions of the factories and suppliers.
- Implementation of programmes at the local level. Since the Agreement was signed, over 80 factories have been the subject of specific training and worker representation programmes.
- Promotion of initiatives that favour decent wages. At Inditex, we work with IndustriALL and other brands on initiatives such as ACT (Action, Collaboration, Transformation) whose objective is to address the issue of living wages in the textile and clothing sector by improving the conditions for dialogue and collective bargaining.
- Joint interventions to address labour issues that may arise in the supply chain.
Throughout 2016, under the umbrella of the Framework Agreement, programmes have been implemented in 21 factories of our supplier clusters, involving 18,634 workers. The programmes have covered numerous initiatives of different kinds with the defence of workers' rights at its core and are organized around three main areas:
- Strategic projects to raise awareness of the rights and responsibilities of workers and employers.
- Programmes to improve working conditions and social dialogue.
- Remediation and accompanying actions.
Factories involved in IndustriALL programmes

II. LIVING wages
Achieving decent wages for the more than one and a half million workers in our supply chain is a key goal of the textile industry as a whole. The actions that Inditex performs in this matter revolve around them.
At Inditex we conceive the living wage as an adequate remuneration that allows workers to cover their basic needs and the needs of their families. This concept is present in our Code of Conduct for Manufacturers and Suppliers. And it is mandatory for them to comply with it by virtue of Inditex’s Minimum Requirements, which they sign as an indispensable condition when they join our supply chain.
Evolution of compliance with the Code of Conduct on wages in active factories (%)
Promoting collective bargaining
The role of workers’ representatives is essential for improving conditions in factories, not only in the area of wages but also in the different aspects of a collective agreement. As a result, a wage and, in general, decent working conditions are those that have been negotiated and agreed between employers and the freely-elected workers’ representatives.
To achieve this, Inditex carries out training programmes for workers and facilitates the election of their representatives through the Framework Agreement with IndustriALL. In this regard, in 2016 training was carried out in three factories in Turkey with over 800 workers benefiting. The democratic election of 32 workers' representatives was also favoured at four factories in Bangladesh.
Responsible purchasing practices
Inditex understands responsible purchasing practices as necessary for compliance with the Code of Conduct, so that they do not impair, not only this Code or applicable law, but also the necessary respect for Human Rights.
To this end, in recent years Inditex has trained buyers in internal regulation and regulatory compliance in sustainability; we have also given them practical tools to make purchasing more sustainable and that favours those suppliers with the greatest degree of compliance in social and environmental issues.
In this regard, 729 buyers have received in 2016 the so-called PrINciples training, which continues in 2017 with the IN Practice workshops, designed ad hoc for the Inditex purchasing teams.
Thanks to this, the purchase from suppliers with the highest social ratings (A or B), in 2016 accounted for 95% of the total, which shows how the purchase has been oriented correctly in favour of suppliers with a hightest degree of sustainability compliance.
Percentage evolution of purchase in suppliers A or B
IMPROVED WORKING METHODS AND SYSTEMS
Improving working methods and systems is one way of improving the working conditions of workers. Taking part in the ILO Score Project in China (and soon in Turkey), as well as implementing the Lean Project in China, have yielded satisfactory results that highlight the scope for improvement currently existing in two of Inditex’s key clusters.
Collaboration with other stakeholders
Collaboration with other stakeholders is essential for improving the conditions of workers in general and, in particular, for achieving decent wages in the industry.
The factories that work for Inditex also do so for other brands, making collaboration with them fundamental for ensuring that the worker is properly paid for his or her work.
In this regard, the ACT initiative is as an agreement between brands and workers' representatives to establish a cooperation that promotes the attainment of living wages in the industry.
Inditex's participation in ACT and its working groups is very active. During 2016, the initiative has become a foundation with the same objective: to transform the industry and achieve decent wages in the sector through collective bargaining. This objective is addressed from three parallel working groups, with collective bargaining as the central axis plus two other groups on productivity and good purchasing practices.
Support campaigns
Finally, the public campaigns in favour of living wages are noteworthy; these evidence Inditex’s commitment to this cause. The last and most notable of these campaigns in 2016 took place in Bangladesh, where, along with other brands, a letter was sent to the country's Prime Minister, Sheikh Hasina, on 4 January, urging, among other things, the adoption of a wage review mechanism that could give stability to the industry in the country.
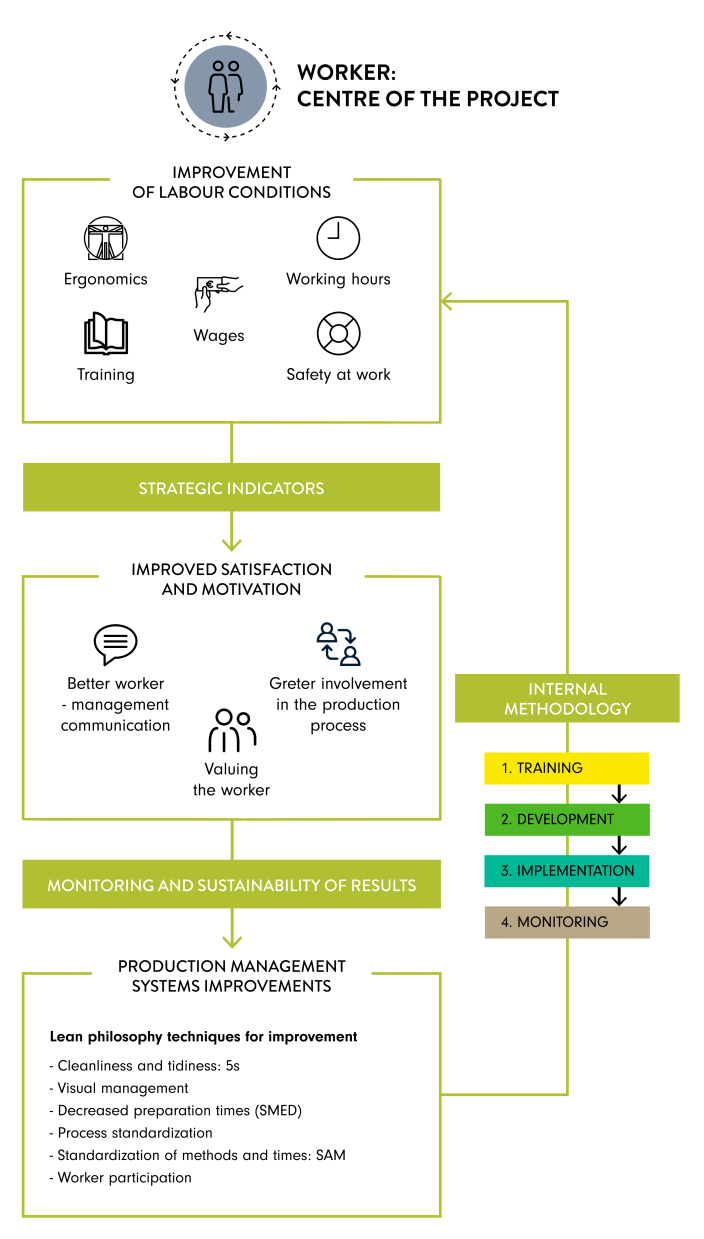
III. Responsible purchasing practices
At Inditex, our purchasing practices include everything from purchasing planning to traceability of the supply chain. For this reason, developing responsible purchasing practices has a direct impact on our supply chain.
The responsible purchasing practices strategy is based on two fundamental premises: our corporate culture and the linking of purchasing decisions to sustainability criteria. With respect to our corporate culture, we foster sustainability in all our internal and external actions. And regarding purchasing decisions, if a supplier’s performance does not meet our sustainability criteria, our systems do not allow us to assign orders to them. To ensure a responsible purchase we use different tools:
- Production traceability: Inditex is committed to the sustainability of its supply chain and for this reason it is essential to identify all those involved in it.
- Evaluation of potential suppliers (Pre-Assessment): Inditex buyers are guaranteed that all suppliers receiving orders have passed a previous sustainability assessment.
- Visibility of the supplier ranking: The purchasing teams have complete sight of compliance with social, environmental and health of the product standards with the objective of placing orders with those with greater compliance in these areas.
- Supplier training: Continuous development of supplier training to improve factories is part of our commitment to stable relationships with ethical and responsible suppliers.
- Code of Conduct and Responsible Practices: The strict internal policy on conflicts of interest and corruption helps to foster ethical and transparent relationships and includes a Whistleblowing Channel.
These tools are complemented by a thorough and regular training process for the purchasing teams of each brand, given by the sustainability teams. In this regard, during the last year training sessions were held with 729 members of the purchasing teams and their managers, as well as 164 employees at headquarters and 112 from the subsidiaries.
This first phase of training sessions called PrINciples aims to promote values, behaviours and the principles of our responsible purchasing strategy. We also train sustainability teams in each brand of the group to ensure the continuity of training to any new purchase-related employee.
In addition to these internal initiatives, Inditex's active participation in ACT's responsible purchasing practices working group is enabling the development of responsible purchasing practices in the industry.
Evolution of employees trained in Sustainability
employees trained in awareness of responsible purchasing practices
IV. Women empowerment
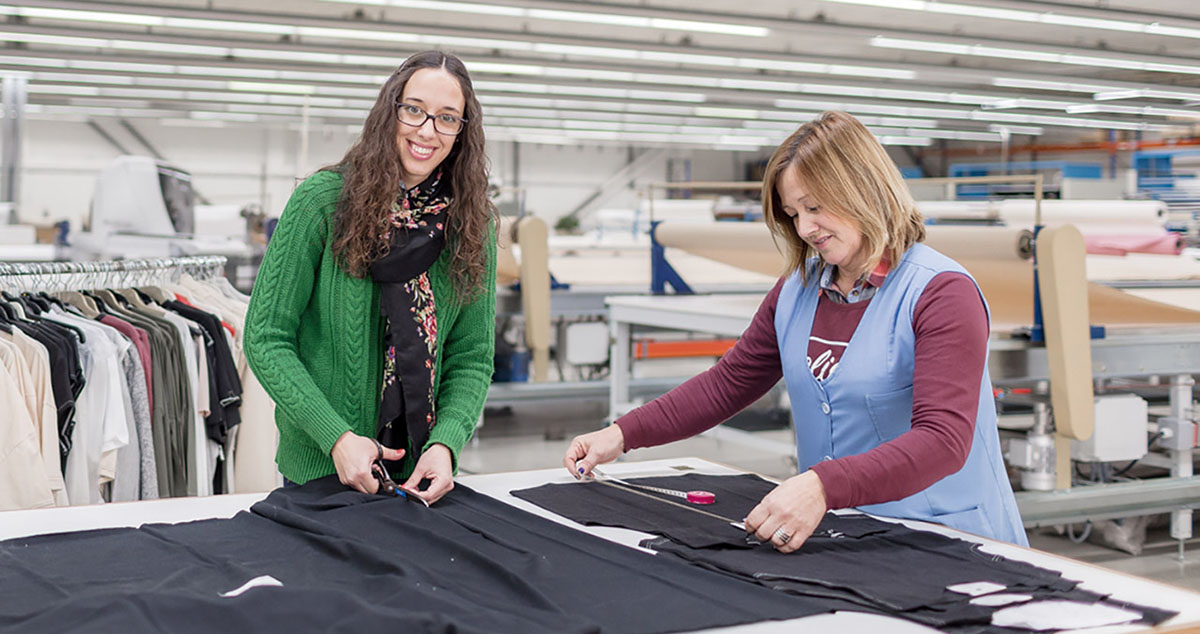
The textile industry is a mainstay of the economy in many of the countries where we operate, and women occupy most of the jobs in all stages of production. For this reason, Inditex's supply chain is mostly female. And it is our duty and mission to contribute to all these workers having the best working conditions and enjoying the same opportunities as a man.
To ensure greater equality for women, we have developed a number of programmes aimed at eradicating gender inequality and strengthening women’s empowerment. All seek to respond to the real needs and social context of women in the countries where we produce, as well as to develop and deepen the work of social audits, as our internal methodology includes tools to identify and evaluate issues related to equality of women in the work environment.
To this end, in 2016 we started a pilot project in Turkey with a factory of 250 workers. In this initial phase, analyses have been carried out to understand the possible causes of gender discrimination in this country. With the findings obtained, the second phase of the programme will be launched in 2017 with the aim of improving the quality of life and working conditions of working women and achieving a full awareness by the factories’ managers.
Also, several years ago we launched a project in Morocco in collaboration with the NGO Medicus Mundi Andalucía, which has provided medical care and treatment to 577 women in Tangiers and has trained workers in health issues in six factories.
Another priority country in this area is India. During 2016, we conducted our Sakhi Project (Sakhi means “friend” in Hindi) which is structured in two parts: Sakhi Health and Sakhi Gender Equity. Both cover two fundamental aspects of the situation of women in the Asian country: health and the prevention of situations of harassment or abuse.
The Sakhi Health Project is a women's health training programme on issues such as nutrition, hygiene, menstrual health, cancer, AIDS and ergonomics. Its objective is to sensitize workers, supervisors and factory management to avoid and prevent future health problems. The future focus of the programme will be to achieve lasting positive change in the lives of workers, with periodic conferences in which all factory educators can take part, discuss difficulties and share good practices in the search for collective solutions.
With the Sakhi Gender Equity Project we are working to identify and prevent situations that may lead to harassment, discrimination or abuse towards female workers. In collaboration with stakeholders, the first step is to develop a comprehensive guide to worker well-being, which will focus on migrant and women workers. Moreover, efforts will be made to create appropriate grievance mechanisms in factories, strengthen representative committees and strengthen systems for the prevention of violence against women at work.
Sakhi-Health | Sakhi-Gender Equity | |
goals |
|
|
Involved stakeholder groups | St. John’s National Academy of Health Sciences (Bangalore) | Swasti, Health Resource Centre |
N° of factories involved | 2 | 4 |
Number of workers reached | 740 | 3,550 |
Achievements 2016 | The programme has been implemented in two factories with great success and its objectives have been achieved. It is scheduled to be fully implemented at the start of 2017. | A study was carried out on women workers in collaboration with other brands, as an example of a collective effort to discover and analyse the roots of the issue. The study allowed the implementation of new and improved practices in the factories. Moreover, a consultation was held with suppliers in Bangalore with the collective aim of creating an anti-discrimination and anti-harassment guide for female workers. |
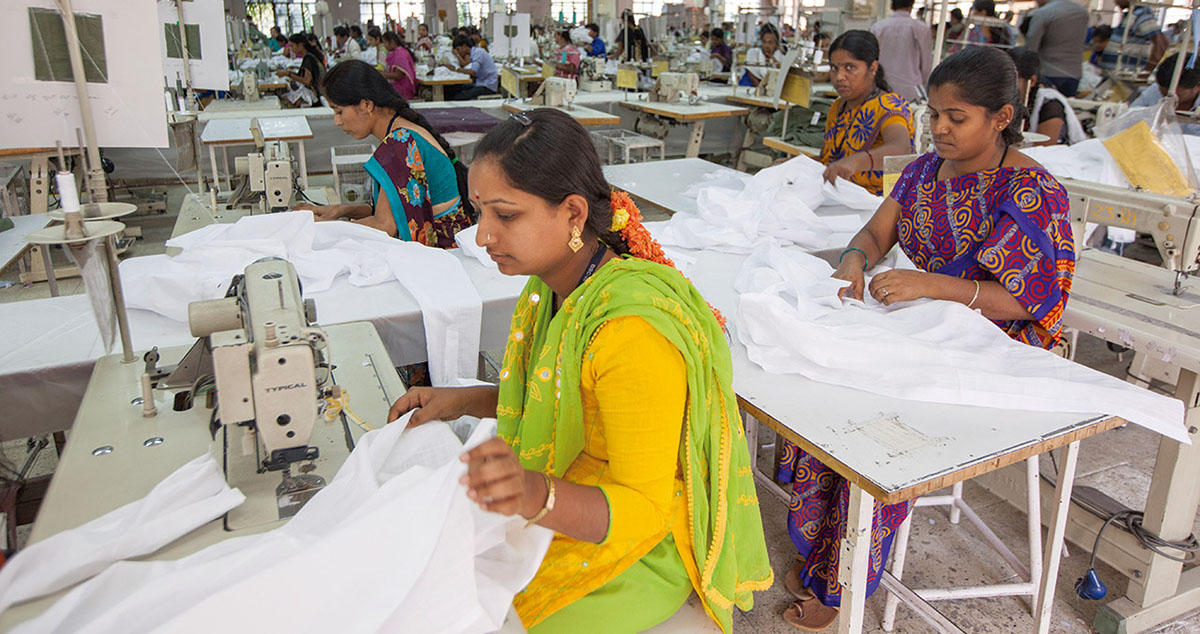
V. OCCUPATIONAL HEALTH AND SAFETY
At Inditex we guarantee safe and healthy working environments for all the workers who are part of our supply chain. This commitment can be seen in the design and implementation of specific programmes that complete the work to verify workers’ health and safety conditions, as well as the establishment of Corrective Action Plans under the Code of Conduct Compliance Programme.
The sustainability teams consistently accompany suppliers and manufacturers to ensure the workers’ welfare , for doing this internal capacity building in matters related to health and safety is fundamental. Indeed, the work of the engineers of our sustainability teams in each country, who provide knowledge and technical skills, is essential.
The programmes reached over 320,000 workers in five countries in 2016, ranging from training actions to specialized risk assessments and establishment of workers' committees. In this way, we address the health and safety of workers in a comprehensive manner.
The different programmes we describe below are a demonstration of our commitment to occupational health and safety in our supply chain, a discipline on which we work consistently with different stakeholders. These programmes complement the various monitoring, evaluation and optimization actions that our internal sustainability team perform in the different clusters.
Morocco
Project for evaluation, continuous improvement and training in health and safety
Throughout 2016, our Moroccan sustainability team developed a project, which began at the end of 2015, for the continuous improvement of health and safety conditions in the Inditex supply chain in Morocco.
The initiative involves the main suppliers –who handle over 75% of our purchase in the country– and, as a first stage, involves the evaluation and identification of aspects of improvement of all the factories that they declare for Inditex productions.
The second phase begins after the evaluation, and action plans are defined, in which the involvement of suppliers is fundamental. At the same time, follow-up visits are regularly carried out to verify compliance with the action plans and, moreover, monthly reports of the progress of the factories are required from all suppliers.
In order to facilitate project progress, the local team has internally designed tools for information synthesis and reporting, allowing the generation of reports tailored to each stakeholder: factories, suppliers and sustainability team.
The main areas evaluated, monitored and optimized in the factories are:
- Workers’ labour conditions
- Conditions of the building where the factory is located
- Facilities and materials: Electricity, machinery and boiler safety
- Chemical and physical agents
- Fire extinguishing equipment and escape routes
- Management system
This project has been carried out in 114 factories of 29 suppliers and has improved the health and safety conditions of 28,318 workers. During this time, the factories and suppliers involved have been in continuous contact with the sustainability team, receiving training on occupational health and safety and clarifying doubts.
Based on the good results obtained, by the end of 2016 the Moroccan sustainability team extended this project to the Inditex supply chain in Tunisia and Egypt, where the evaluation of the factories has already begun. The project continues in 2017.
Bangladesh
Monitoring Compliance with Accord Corrective Action Plans: FIRE PREVENTION and electrical safety and structural evaluation
Inditex is a signatory of the Accord on Fire and Building Safety in Bangladesh, better known as the Accord, since its inception in 2013. Under this legally binding agreement, its members, (international brands, local and international trade unions and various NGOs) are committed to improving the health and safety conditions of the factories of the sector in the country.
In this regard, all the production units under the scope of the Accord that are part of the Inditex supply chain in Bangladesh have been inspected by this organization’s engineers in matters relating to structural, fire and electrical safety. These inspections generate public Corrective Action Plans, drawn up by the Accord and the factory, and which must be implemented in collaboration with the international brands associated with these factories.
Inditex is firmly and actively committed to these plans as a fundamental aspect of the Accord inspection and remediation programme, since they guarantee compliance with this organization’s health and safety standards and its implementation is officially verified by its teams of monitoring inspection engineers.
In collaboration with external structural, fire and electrical safety experts, Inditex's internal team of engineers completed a total of 523 monitoring inspections in 2016 to complement the Accord inspections and ensure the correct and timely implementation of the necessary measures in the factories.
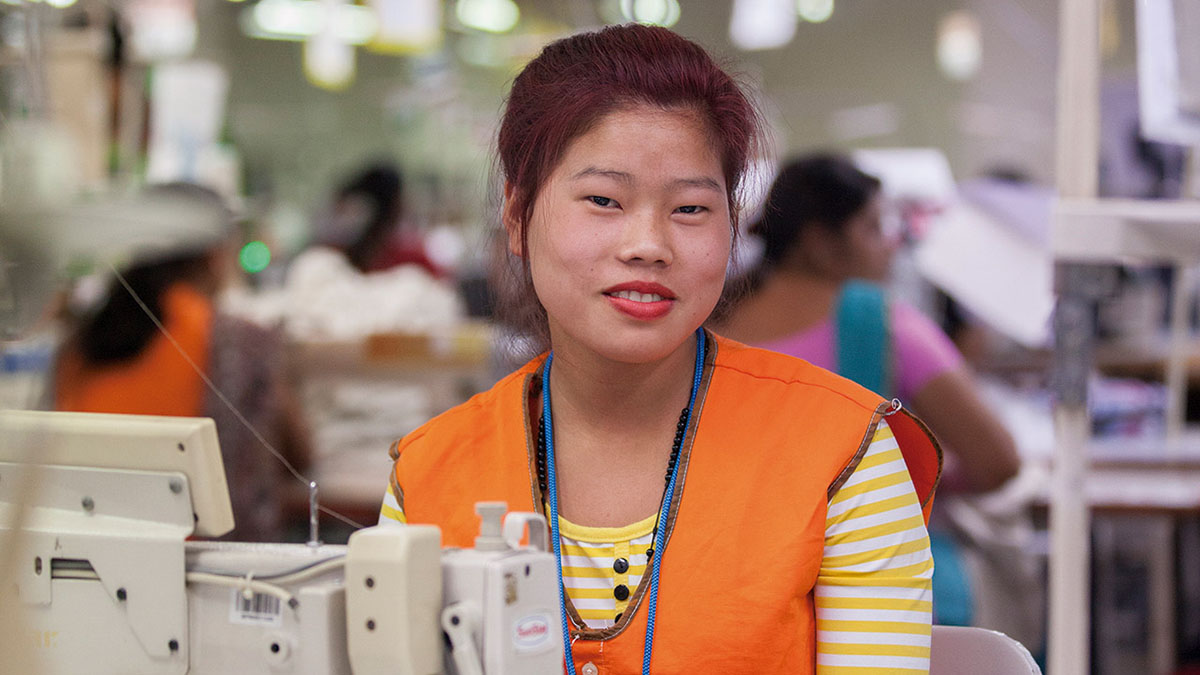
Guía para la correcta evaluación de las estructuras de los edificios
As part of the 2016 initiatives in Bangladesh, we have worked with an international engineering consultancy to develop a guide for evaluating building structures in depth.
Preparing this manual was part of a pilot project in six factories in our chain. Its objective is to develop an efficient methodology that takes into account the characteristics of the country in terms of the structural characteristics of its industrial buildings.
The guide was presented to the Accord and other relevant local and international entities in Bangladesh; this is the culmination of a project to facilitate structural evaluation through standard and comprehensive methodology.
Participation committees as the basis of health and safety committees
Workers’ participation and representation in matters of health and safety is one of the fundamental aspects recognized internationally in this discipline. In particular, the establishment of health and safety committees in textile factories in Bangladesh is one of the main axes on which the Accord is based, as defined in its worker participation programme.
Inditex has worked actively with the Accord in this programme, which includes training sessions for health and safety of workers, the creation of a whistleblowing channel for these issues and the creation of health and safety committees to ensure the workers’ participation in maintaining a safe and healthy environment in the factory.
At the same time, the Inditex sustainability team in Bangladesh undertook, as part of the Global Framework Agreement with IndustriALL, a pilot project to promote the effective formation of workers’ participation committees through the free election of their representatives in a democratic vote. It is important to mention that, according to Bangladeshi legislation, members of health and safety committees are elected by the workers' participation committees of the factories. This project has been implemented in four factories in the Inditex supply chain and around 4,000 workers have taken part.
Technical evaluation for new suppliers and manufacturers
As part of the process of incorporating new suppliers and manufacturers into our supply chain in Bangladesh, we carry out strict technical assessments in occupational safety and health, to verify that all production is carried out in safe installations.
In this regard, the Inditex sustainability team’s engineers in Bangladesh have developed a technical assessment methodology to perform standard inspections on these units. In this way, they identify and evaluate the potential associated risks and guarantee safe and healthy conditions in all the factories of the supply chain in the country, regardless of whether or not they are inspected by the Accord.
In 2016, 47 technical evaluations of factories were carried out, which allowed the verification of the work environments of around 40,000 workers.
India
HEALTH AND SAFETY ASSESSMENT AND TRAINING PROJECT
At the end of 2016, the Indian sustainability team started a project to assess occupational risks and training in Inditex’s supply chain factories. In this way, the factories have the means and tools to carry out a complete and regular risk assessment. The willingness to complement the Indian legislative framework on occupational health and safety for industrial workers has been one of the aspects that has driven this project.
The project is divided into three modules that are conducted in the facilities of the manufacturer involved. These define the responsibilities of management on these issues and introduce analysis tools. Moreover, the risks present in the factory are evaluated and corrective actions are defined that reduce their severity and probability. The company’s own health and safety officers then proceed to conduct a complete risk assessment and to define corrective actions in agreement with the sustainability team.
At present, this project involves three suppliers and six factories and benefits 3,040 workers. The goal is to extend it to a greater percentage of suppliers and manufacturers.
CHINA
Internal and external training in health and safety and RISK assessment of suppliers at their factories
In 2016, the EHSA Centre of the University of Ling’nan in Guangzhou (China), specializing in environment and occupational health and safety, gave various trainings to the China sustainability team in:
- Legislation on Occupational and Environmental Health and Safety
- Ergonomics and occupational health and safety management systems
- Electrical and machinery safety
A more ambitious project emerged from these sessions with the university to improve health and safety conditions in our supply chain in China. The starting point has been the training of suppliers according to an agenda developed from an analysis of the aspects with the greatest potential for improvement of the main suppliers in the country. According to this work, a group of 28 suppliers from Guangzhou and 34 suppliers from Shanghai have been trained in:
- Fire prevention
- Machinery safety
- Electrical safety
The next steps in the project have focused on involving suppliers to apply what they have learned to their factories. Subsequently, the Chinese sustainability team worked with the participants on identifying and assessing risks and designing Corrective Action Plans whose ultimate goal is to improve health and safety conditions in our supply chain.
vietnam
Monitoring of the structural SAFETY of buildings
The tasks of accompanying suppliers and manufacturers in all clusters of our supply chain to optimize the levels of compliance with aspects related to occupational health and safety led the Vietnam sustainability team to monitor the structural improvements made in six factories in 2016.
These monitoring tasks resulted in visits to factories to review progress. In this process, external engineering firms collaborated with the Inditex teams to verify and guarantee improvements in these facilities.
turquía
Technical training with the Fair Labour Association Turkey
In 2016, Inditex’s Turkish sustainability team took part in advanced technical training, given by mechanical engineers linked to the Fair Labour Association Turkey, an organization that also participated in the design of content and the delivery of these trainings.
The content of this training was oriented towards themes such as physical risk factors, chemical risk factors, ergonomics or working at height, among others.
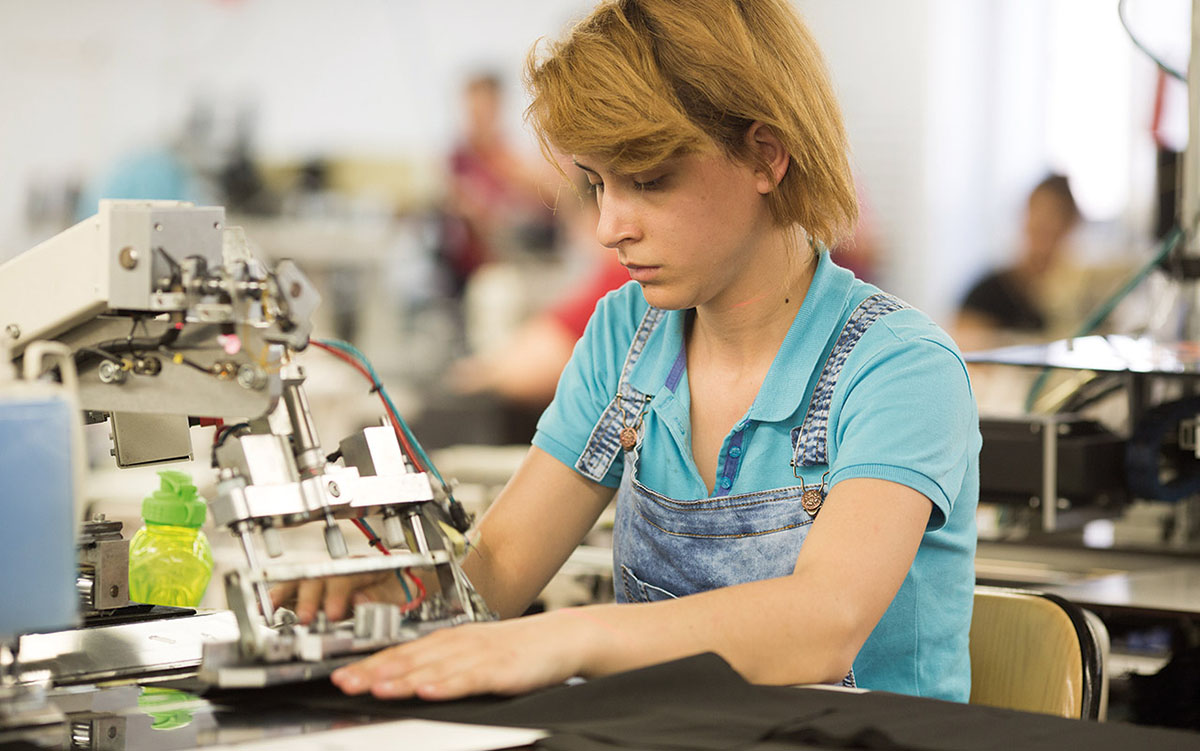
Looking to 2017, we have launched new programmes to continue working for the continuous improvement of health and safety in our supply chain. In this regard, we have initiated a project in Cambodia in cooperation with 23 industry brands, the government of the country, the American Centre for International Labour Solidarity, the Better Factories Cambodia Programme and the Deutsche Gesellschaft für Internationale Zusammenarbeit. The aim of the project is to reduce in-itinere accidents suffered by textile workers.
VI. Protection of migrants
Inditex faces the complex challenge of migration by maintaining a Zero Tolerance policy towards any exploitation in its supply chain derived from this situation, as set out in the Code of Conduct that all manufacturers who work with us must meet. In 2016, we would highlight our programmes in Turkey and China.
The migratory flow of the more than five million people who have been forced to flee the armed conflict in Syria to Europe has generated a humanitarian drama unprecedented in recent history. The exodus of refugees has affected not only governments, supranational organizations and NGOs, but also businesses, which have the ethical duty to act and work as much as possible to improve the situation.
The Group gives special protection to all migrants, which includes refugee workers in connection with the conflict in Syria because of their situation of greatest vulnerability. Those in this situation may be exposed to irregular working conditions, discrimination, excessive hours or inadequate wages. In this scenario, Inditex carries out rigorous analyses to identify migrant workers and evaluate their employment status as an essential step in creating programmes and initiatives that protect them and have a real effect on their conditions.
Turkey is one of our main supplier countries and it is currently estimated that about three million displaced Syrian people live on its territory. In response to this humanitarian crisis, Inditex was the first company to launch a remediation plan dedicated to supporting Syrian refugee workers in Turkey to prevent any type of exploitation. Specifically, since 2013, when the crisis worsened, we have intensified our efforts to prevent any violation of their Human Rights in our supply chain. In addition, to ensure that refugees have fair working conditions and rights, we work with the non-profit Refugee Support Centre/MUDEM.
MUDEM helps us to treat each case individually, informing workers of their rights and advising them to legalize their employment status in Turkey. It also teaches them Turkish and translates the necessary documents for their adaptation: regulations, procedures and aspects of health and safety, among others.
The plans have been very effective in helping Syrian workers to legalize their work status, and to improve their living conditions and those of their families. In 2016, we initiated 131 individual remediation cases, addressing the needs of each worker and their families.
In 2016 we also established programmes for internal migrants in China, focused on ensuring that they understand and receive the social benefits to which they are entitled. In 2015 we helped prepare an information guide in this area and currently, we are taking part in a project that aims to provide training and awareness to suppliers and the workers themselves, with the Ethical Trading Initiative.
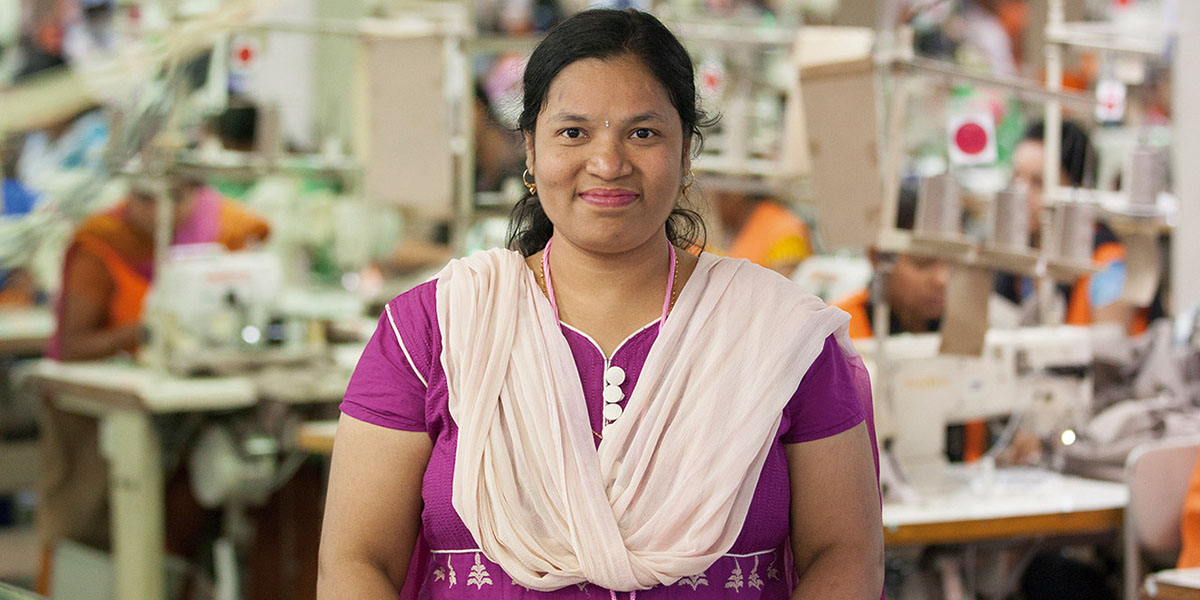
VII. Training and awareness
The training and awareness of all the actors involved in the supply chain is fundamental to guarantee its sustainability. Inditex applies this maxim by training suppliers, manufacturers or auditors, whose relationship with the supply chain is more direct and evident, but also its employees, regardless of their area of work. The Group invests in training all the necessary people, adapting each type of training to the needs of the target group, as a fundamental step to ensure that sustainability and respect for Human Rights are fully integrated into the business model.
Main recipients of Inditex training
MAIN RECIPIENTS
OF INDITEX TRAINING
Internal and external auditors
In 2016, Inditex worked with 720 external auditors and 63 internal auditors to ensure that all suppliers and manufacturers in the supply chain comply with the Code of Conduct and establish Corrective Action Plans where cases of possible defaults are detected.
Continuous training is essential for auditors to carry out their work in the most effective and efficient way possible; through their audits, Inditex seeks verification of compliance with the standard, but it is also a tool to raise manufacturers’ and suppliers’ awareness of the need to comply with the Code of Conduct and how to correct any breaches.
To this end, we train our internal and external auditors in Inditex's own methodology and in best auditing practices. In 2016, training for external auditors addressed specific issues such as worker health and safety requirements, freedom of association and bargaining, auditing techniques focused on verification through non-documentary sources, traceability and continuous improvement of the audit itself.
The members of Inditex’s internal auditor team are accredited by Social Accountability International (SAI) as auditors able to verify compliance with the SA8000 standard, which is based on standards such as those established in the Conventions of the International Labour Organization, the United Nations Universal Declaration of Human Rights, and UN Convention on the Rights of the Child.
Employees
All employees participate in the Group’s sustainability strategy, because at Inditex we are aware that, if sustainability is to be a maxim in the daily activity of each employee, we must convey the company’s position and train them in the subject. Thus, all new employees at headquarters receive training on sustainability and company's strategy and key concepts such as the Code of Conduct for Manufacturers and Suppliers and what the Compliance Programme consists of.
Inditex emphasizes the training of purchasing teams among all employees, as their decisions affect the conditions of supply chain workers, and a Responsible Purchasing Practices training system has been developed.
Whenever a training need is identified with respect to a relevant sustainability and human rights issue, sustainability teams develop and deliver specific training.
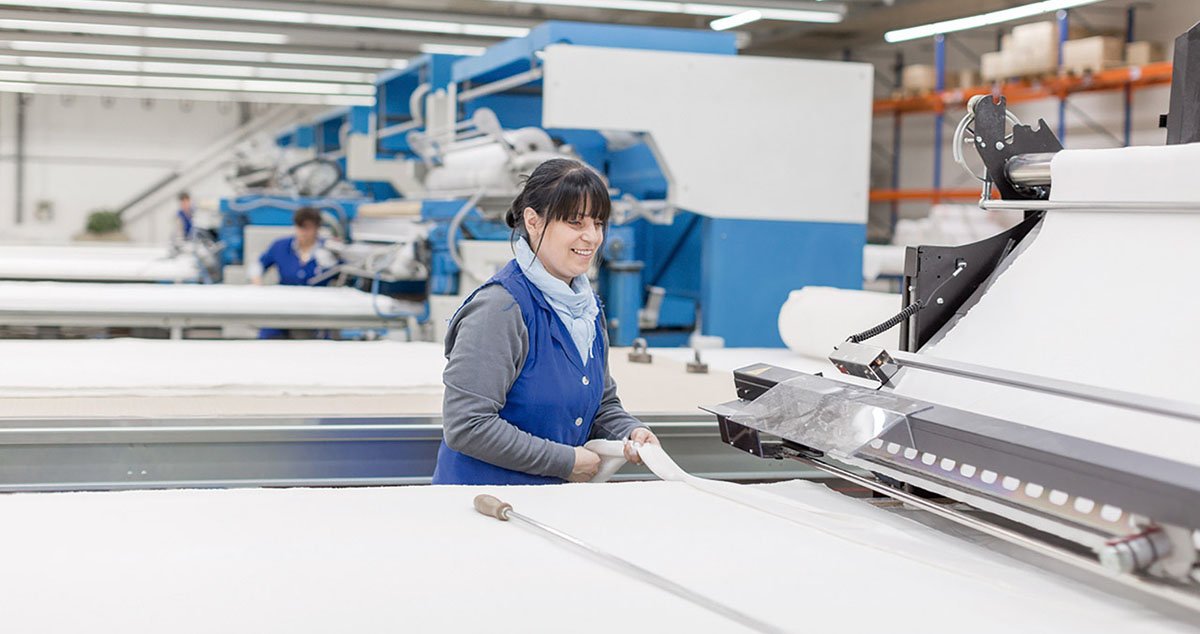
Suppliers and manufacturers
Continuous improvement is one of Inditex's fundamental approaches to its sustainability strategy which, in the case of manufacturers and suppliers, translates into a commitment to their training and preparation.
To strengthen compliance with the Code of Conduct for Manufacturers and Suppliers, it is an indispensable condition that they all know the Code’s contents, understand and internalize them and assume them as their own before applying them. And training is a key tool for this.
Training activities are continuous in all clusters. Each training is tailored to the needs of each cluster, taking into account parameters such as local legislation, specific opportunities for improvement in each country, or their own situation whether as a new supplier or with a lengthy relationship with Inditex.
In 2016, training of suppliers in aspects such as freedom of association and collective bargaining, traceability, improvement of workers’ conditions based on changes in factory production management systems, health and safety, children’s rights or systems of self-monitoring of the supply chain by the supplier was noteworthy.
In addition to the group trainings, our sustainability teams conduct individual sessions with suppliers, maintaining a dialogue that enables joint and proactive supply chain management. This also facilitates working to remedy detected non-compliance and favours the continuous improvement of the workers’ conditions.