2. Assessment of the supply chain
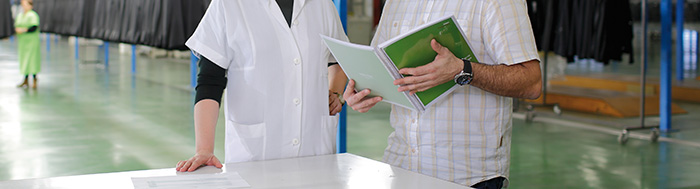
Social audits |
Supplier classification |
Production audits |
Corrective action plans |
ASSESSMENT (highlights in 2013) |
The Compliance Programme ensures that all suppliers of the Inditex Group observe the Code of Conduct for Manufacturers and Suppliers. The Programme has different assessment tools that allow full analyses to be made of the supply chain, identifying its strengths and needs.
Social audits
Each and every supplier in the Inditex supply chain is subject to periodic social audits. The aim is to verify their compliance with the Code of Conduct and to establish Corrective Action Plans (CAPs) intended to ensure that fundamental labour rights are respected.
Further information at http://www.inditex.com/en/sustainability/suppliers/csr_audits
In 2013, the number of audits increased by 24% compared with the previous year, mainly due to an increase in special audits which consisted of visits and inspections related to specific issues such as the health and safety of workers, and competence visits to ensure compliance with the Corrective Action Plans. These audits include, for instance, the inspection of laundry processes to ensure that the sandblasting process, which is prohibited by Inditex, is not in use.
The audits are performed on all levels of production and are carried out both by internal auditors and certified external auditors, without prior notification of the date the visit is to be performed.
Further information at http://www.inditex.com/en/sustainability/suppliers/compliance_programme
Audits performed on manufacturers in 2013 by geographic area and type
Geographic area | Initial | Follow-up | Special (*) | Total |
Africa | 120 | 43 | 244 | 407 |
America | 261 | - | 238 | 499 |
Asia | 994 | 172 | 1 120 | 2 286 |
Europe (non-EU) | 543 | 65 | 14 | 622 |
European Union | 502 | 48 | 3 | 553 |
Total | 2 420 | 328 | 1 619 | 4 367 |
(*) Special audits include competence visits, Health and Safety verification, among others.
Living wage
As expressly established in the Code of Conduct for Inditex Manufacturers and Suppliers, the company considers a living wage one which is “sufficient to cover at least the basic needs and any other that might be considered reasonable additional needs of the workers and their families”. As a result of its monitoring work, the CSR team has detected that in some regions, the minimum legal wage is not sufficient to cover these needs. It therefore considers it a priority to establish joint measures with stakeholders to eliminate these differences.
For Inditex, assuring a living wage for all workers is one of the pillars of the management of its supply chain. In this sense, the company focus is based on facilitating the participation of all parties involved. From its experience, Inditex believes that such participation is the way to generate sustainable measures adapted to workers’ real needs.
In the context of the Framework Agreement with the IndustriALL Global Union, Inditex encourages social dialogue to ensure that a living wage is agreed between workers and business owners through collective bargaining. To this end, Inditex has implemented programmes to promote freedom of association and make it possible to reach agreements. One example is the Joint Turkey Programme, an innovative programme that seeks to improve productivity and management systems by involving workers and their representatives. Other programmes to enhance social development were carried out in 2013 in the clusters in Portugal, Morocco, China, Argentina and Brazil.
Inditex also forms part of a working group created in 2013 by the Ethical Trading Initiative, in which it played an active role in drawing up general principles allowing wages on the supply chain to be increased. By adhering to these principles, the company undertakes to ensure that its purchasing practices favour living wages throughout the supply chain.
Supplier classification
The social audits assess the suppliers’ compliance with each and every section of the Code of Conduct. According to the results obtained, specific areas are identified for improvement in order to ensure the fundamental labour rights of workers and guarantee product compliance with environmental and health and safety standards.
2013 | 2012 | |||
Supplier | % Supplier | Supplier | % Supplier | |
A | 697 | 44% | 525 | 37% |
B | 614 | 39% | 617 | 43% |
C | 128 | 8% | 157 | 11% |
PAC (*) | 82 | 5% | 72 | 5% |
PR (**) | 71 | 4% | 63 | 4% |
Total | 1 592 | 100% | 1 434 | 100% |
(*) Suppliers subject to a Corrective Action Plan.
(**) Suppliers under audit.
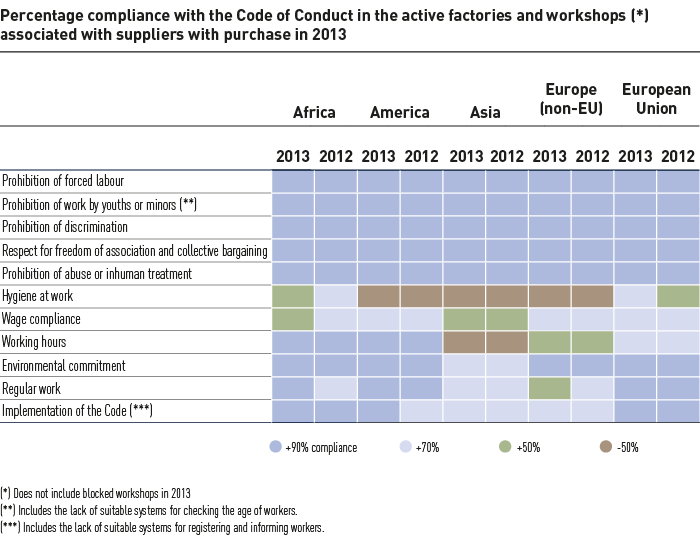
The high percentage of compliance with the Code of Conduct on the part of manufacturers with a relationship with Inditex reflects the efforts of the CSR teams and other members of the clusters to strengthen the supply chain.
The first phase of the implementation of the new methodology for checking workshops was carried out in 2013. This involved the application of more and better controls.
Corrective action plans (CAP)
After every audit, Inditex establishes Corrective Action Plans and supports and advises each factory on their application. These Corrective Plans are particularly strict in the case of factories that have committed certain breaches of the Code of Conduct. In such cases, plans are established for up to six months and are supervised by Inditex teams on the ground with the participation of institutions such as trade unions and NGOs where necessary.
In 2013, a total of 249 of the factories on a Corrective Action Plan successfully performed the necessary measures and continued to produce for Inditex.
Corrective Action Plans 2013 (Project D)
Geographic area | Factories that initiated an improvement process |
Factories that improved their compliance |
Factories in the process of improvement |
Africa | 31 | 23 | 5 |
America | 16 | 11 | - |
Asia | 274 | 105 | 48 |
Europe (non-EU) | 197 | 98 | 14 |
European Union | 50 | 12 | 12 |
Total | 568 | 249 | 79 |
Inditex promotes the continuity of the suppliers in any case, helping them to guarantee workers’ fundamental labour rights, but has zero tolerance with manufacturers or suppliers who fail to show progress in improving critical aspects of the Code of Conduct.
If, after the application of one of these plans no improvements are observed, the Inditex purchasing and CSR teams will suggest the suspension of commercial relations with the supplier.
Table of active suppliers at 31/01/2014
Geographic area | Nº of Suppliers | Rejected due to breach of the Code of Conduct |
Rejected for commercial reasons |
Active suppliers at 31/01/2014 |
Africa | 124 | 1 | 2 | 121 |
America | 82 | 19 | - | 63 |
Asia | 738 | 56 | 2 | 680 |
Europe (non-EU) | 151 | 13 | 1 | 137 |
European Union | 497 | 10 | 9 | 478 |
Total | 1 592 | 99 | 14 | 1 479 |
Production audits
The production audit is one of the tools available to Inditex to guarantee the traceability of its supply chain, reinforced during 2013. Production auditing verifies the following aspects:
Verified aspects | Verification method | Auditing tools |
Processes | Verification that the supplier has reported all the processes it needs to manufacture a product | Factory Management System, visit to facilities |
Amounts | Verification that the amounts ordered correspond to the workshops’ production capacities | Factory Management System, visit to facilities, documentary check |
Times | Verification that the required manufacturing times can be assured with the resources available to the supplier | Factory Management System, visit to facilities, documentary check |
Management systems | Assessment of the management systems the company has for dealing with its production | Interviews, documentary revision |
Other aspects | These include the supervision of other critical aspects of the Code of Conduct related to is compliance with labour and environmental issues | Visit to facilities, interviews, review of documentation |
In 2013 more than 800 production audits were carried out.
Geographic area | No. of audits |
Africa | 307 |
America | 347 |
Asia | 82 |
Europe (non-EU) | 84 |
European Union | - |
Total | 820 |
Inditex employs a verification system that allows it to identify discrepancies in production audits. If any breach of the Code of Conduct is detected, a Corrective Action Plan would be implemented, aiming at rectifying these. Those suppliers who do not commit themselves to carrying out a Corrective Action Plan or who, after application of one of these plans, do not reach any improvement, would be excluded from Inditex’s supply chain.