B. Audits
In 2012, the number of audits increased 48%
All suppliers that form part of Inditex's supply chain undergo social audits. These are conducted by Inditex's local CSR teams or specialised external auditors within the manufacturers' facilities to assess their degree of compliance with the Code of Conduct for Manufacturers and Suppliers. These social audits, structured around the Code of Conduct, were conducted in accordance with the Tested to Wear methodology, which was jointly designed in 2007 by the International Trade Union Federation, ITGLWF (now associated with the industry's new international federation, IndustriALL Global Union), the Cambridge Centre for Business and Public Sector Ethics and Inditex. This methodology will be extensively reviewed in 2013 so as to include all the modifications and experiences accumulated over the last few years.
More than 91% of the articles produced in 2012 came from Suppliers A or B
These social audits include inspections of the installations, document reviews (management systems, payroll, hours worked, production, worker documentation and permits among others), interviews with factory managers, employees, trade union representatives and health and safety representatives, to name but a few.
Audits conducted in factories and workshops in 2012 by geographical area
|
Initial audits | Follow-up audits | Special Audits* | Total |
---|---|---|---|---|
Africa | 56 | 66 | 101 | 223 |
America | 158 | 6 | 326 | 490 |
Asia | 1,020 | 328 | 271 | 1,619 |
Non-EU Europe | 478 | 101 | 154 | 733 |
European Union | 301 | 107 | 40 | 448 |
Total general | 2,013 | 608 | 892 | 3,513 |
In 2012, the consolidation of the local CSR teams meant an increase of 48% in the number of audits conducted in comparison with the previous financial year.
For more information on the audits conducted per country, see the Sustainability Balance Sheet.
During the 2012 financial year, 3,513 audits were carried out on manufacturers and suppliers
As a result of the social audits, suppliers are classified according to their degree of compliance with the Code of Conduct for Manufacturers and Suppliers. More than 91% of the articles produced in 2012 came from Suppliers A or B. The Group’s ultimate objective is for its suppliers to be categorised as A or B.
The different degrees of compliance with Inditex's Code of Conduct for Manufacturers and Suppliers
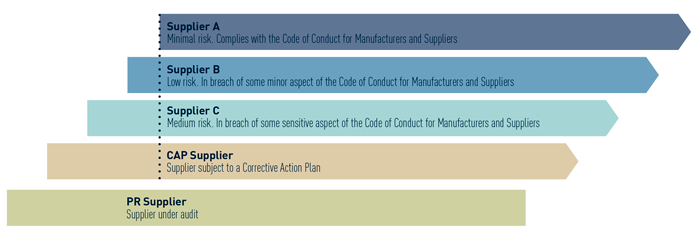
Rating of suppliers used in 2012*
TOTAL | 2012 | 2011 | ||
---|---|---|---|---|
|
SUPPLIERS | % SUPPLIERS | SUPPLIERS | % SUPPLIERS |
A | 525 | 37% | 573 | 39% |
B | 617 | 43% | 501 | 34% |
C | 157 | 11% | 183 | 12% |
CAP** | 72 | 5% | 122 | 8% |
PR | 63 | 4% | 111 | 7% |
Total general | 1,434 | 100% | 1,490 | 100% |
The Group’s ultimate objective is for all of its suppliers to be categorised as A or B
In the 2012 Annual Report Inditex replaced the former “D” rating (supplier in breach of a critical aspect of the Code of Conduct) with the new “CAP” (Corrective Action Plan) rating. This is not merely a question of terminology as it implies a change in perspective and a commitment to improve that is inherent in the programme Inditex has followed for more than 10 years with the aim of strengthening the supply chain. That is to say, all suppliers, especially those included in this new rating, are issued an improvement plan (that they are obliged to implement) which focuses on the most important breaches of the Code of Conduct. This commitment is shared by all parties involved, ranging from the suppliers to the purchasing teams and internal CSR teams. Examples of these plans can be found in the next pages.
More information on supplier ratings can be found in the Sustainability balance sheet.
Continuous improvement of the reliability and quality of the social audits
Within the programme for continuous improvement carried out on all aspects related to sustainability, Inditex places special emphasis on social audits. Thus, during 2012, the Group perfected the visits paid to the production centres in order to provide a high-quality result with greater added value allowing both the suppliers and Inditex itself to function more effectively.
To this end, the Group relied on renowned organisations to train its CSR teams.
Inditex's Training Procedure for External Auditors
In 2012, a new procedure that affects the relationship between Inditex and its external auditors was introduced. Inditex took the initiative to create its own training process so that all external auditors would receive the same standard training thus ensuring an in-depth knowledge of the methodology employed during Inditex's social audits.
Thanks to this training process for external auditors, Inditex can guarantee the social audits carried out on its suppliers and manufacturers are conducted by professionals trained in the standardised processes the Group promotes.
This mechanism makes it possible to standardise the processes involved in social audits using Inditex's parameters in aspects as important as:
- Inditex's CSR strategy
- The compliance programme for the Code of Conduct for Manufacturers and Suppliers
- Inditex's Tested To Wear (TTW) methodology used in social audits
- Priorities in the areas of compliance
- How to correctly perform a TTW audit
During 2012, 113 external auditors were trained using the procedures carried out by Inditex's Department of Corporate Social Responsibility.
Collaboration with Verité
The Verité consultancy organised a variety of workshops specifically designed for the CSR teams with the aim of starting up the “Verité Systems Approach (VSA)”.
The objective of these workshops was to enhance the skills of the auditing teams in aspects such as:
- A study of the existing systems and management procedures for suppliers and manufacturers
- An analysis of the relationship existing between the types of control carried out on manufacturers and compliance with Inditex's Code of Conduct for Manufacturers and Suppliers
- Encouraging interaction with and support for suppliers to help identify and integrate the necessary controls in their management systems to monitor compliance with the Code of Conduct for Manufacturers and Suppliers.
- Work in collaboration with strategic suppliers to develop self-monitoring tools to ensure compliance with the Code of Conduct for Manufacturers and Suppliers
Collaboration with Social Accountability International (SAI)
During 2012, Inditex’s internal auditors were accredited by Social Accountability International (SAI) as SA8000 auditors. This standard is one of the certifications of reference in terms of fundamental labour rights and covers all industrial sectors. It is based on the Conventions of the International Labour Organisation (ILO), UN parameters as well as other national legislation. A specific course was given to impart practical knowledge on all aspects of social audits based on the SA8000 standard.
These aspects included:
- Advanced concepts related to the production line and social audits
- Analysis of the most common difficulties related to non-compliance and possible solutions
- Implementation of more effective auditing techniques
- Creation of methods to correctly detect areas within a factory or on supply chain with room for improvement